ABSTRACT
In cities around the world, the lack of housing is a problem that is expected to grow in the coming decades. The United Nations are estimating that up to 1.6 billion people are lacking adequate housing around the world. In the city of Toronto specifically, the housing problem is very pronounced.
Infinite3 is a project that attempts to provide a easy to build and sustainable housing construction system for the city of Toronto, based on three design drivers: circular materials, Design for Disassembly, and participatory design. The aim is to develop a system that can quickly increase the available housing stock, while generating living units with a high degree of flexibility and customization.
The primary focus of the research has been developing a construction system that adopts the principles of Design for Disassembly. In order to increase the ease of reconfiguring the produced space, the creation of a new system of lightweight wall panels was investigated. This research was combined with physical tests of the connections between the panels and the elements of the structural system.
The proposed solution is a scalable construction system. Glulam columns and beams, fastened with connectors that allow for an easy disassembly, create the structural grid. The floors are constructed with CLT panels. This system can support a variety of different housing types. A system of interlocking panels, made from repurposed byproducts of the timber industry, is used for the partitions of the houses. This allows for easy reconfiguration, change of use, and expansion of the housing units.
Through a participatory design process the residents can take control of designing their own apartments. After the construction of the housing units, the same system can be used for designing expansions and reconfigurations of the space.
The final design proposal can help tackle the housing crisis, by offering short construction times, sustainable materials, and freedom of design to the users. The proposed housing units are easily reconfigurable and adapt to customers changing needs while the end product can be easily disassembled and repurposed.
Project overview
RESEARCH FRAMEWORK
The construction industry has a heavily negative impact on the natural environment. 40% of the materials consumed globally are used in construction. In fact, buildings are also responsible for approximately 40% of the global energy consumption. Additionally, they contribute around 36% of CO2 emissions.
Despite consuming so many resources, the construction industry has failed to keep up with the demand for housing. The United Nations are estimating that up to 1.6 billion people are lacking adequate housing around the world1. This number will only grow, as 37 megacities are expected to have been formed by 2025. In cities like Toronto this housing problem is turning into a crisis.
STATE OF THE ART
RESEARCH
01 Materials
The search of materials starting with an in depth exploration of the natural resources around Toronto, in the province of Ontario and in the wider North American market. The geological and geographical conditions in Canada, have led to the growth of large forests. Canada is one of the foremost timber producers in the world. Ontario and neighboring Quebec are the 2nd and 1st largest producers in the country respectively. As a result, Ontario has a very developed timber industry that produces a wide variety of products. The timber is sourced from sustainably managed forests.
A material of high interest is mass timber. Engineered timber drastically increases the performance of wood and offers a product with much lower embodied energy and carbon footprint than steel or concrete. Mass timber, such as glulam and CLT can be great options for a structural system, for an, interior, reconfigurable system of wall panels, a catalog of upcycled timber waste products was examined.
02 DfD connections
A qualitative comparison of different structural system was performed. The selected systems were ranked based on their ease of disassembly, their expandability, the types of materials they require, the difficulty of construction, as well as their structural reliability. In the end, a combination of two systems was chosen. Both systems have high scores and when combined, will produce a robust structural system with high flexibility.
DESIGN PROCESS
01 Mass timber system
The selected cell dimension is 3,5 m x 3,5 m. This covers Toronto’s minimum space requirements, while the cubic shape ensure interchangeability between the elements of different cells. In the version A of the cell, the metal connectors that were used serve the dual purpose of connecting the columns with one another and connecting the beams. This connector type leaves a game between the two columns, which can be utilized to lock the CLT floor panels in place.
Having a single CLT plate for the floor restrict the possibilities for reconfiguration and vertical expansion of the housing units. For this reason, the CLT was later split into three smaller plates. A new column to column connection was introduced, where the metal connectors is inserted into the mass of the column below. This removes the locking of the floor plates by the columns, and they are now free to be removed at any point, either completely, or partially.
Consequently the beams are attached to the column through a second connector. Connectors of this type can be preinstalled on the columns and the beams before they leave the factory. This significantly decreases the construction time and the complexity of the assembly order. All the elements are completely interchangeable and can be used in any of the cells.
Mass timber cell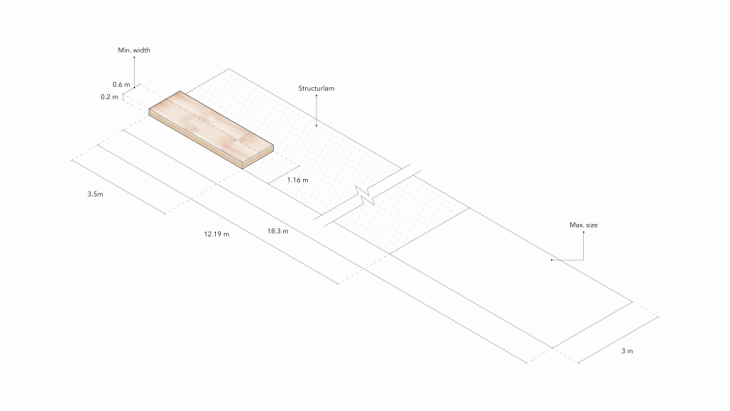
CLT plate size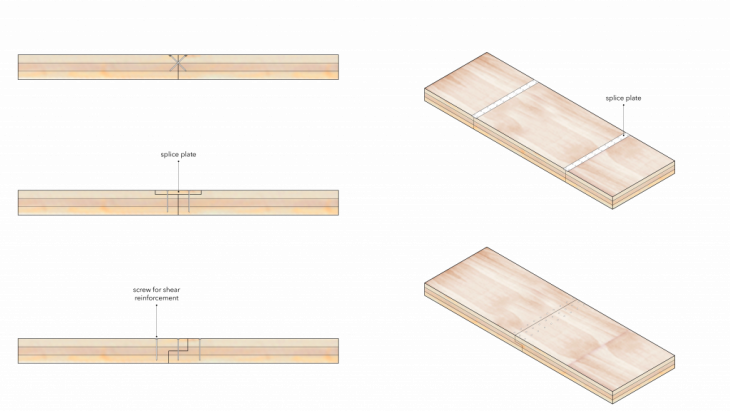
CLT connection detail
02 Wall panels
The standardization of the structural elements through the mass timber system, provides all cells with the same wall dimensions. This feature can be exploited for creating lightweight, easily assemblable walls. By giving ownership of the wall material toy the resident of the housing unit, he is able to endlessly reconfigure and renovate his space. At the same time, a marketplace for wall panels will allow them to be reused as part of expansions of housing unit, in the same or other buildings inside the city.
That goal imposed a strict set of restrictions on the design of the panels. They have to be:
Lightweight: they must be easy to carry around by one person
Human sized: their dimensions should facilitate their transfer and storage by one person
Disassemblable: the disassembly of the wall system must be easy and fast to perform, using only common hand tools.
Expressive: since the wall system will be disassembled, the panel must be able to act as the final wall finish, without compromised in the users ability to customize it.
The version A of the panel is made of two materials. The main body of the panel is constructed using compressed waste pieces of the timber and agroforest industry. The connection between them is realized through an external metal hook and a metal plate, placed within a recess.
Wall panel version A
The version B addresses the shortcoming of the first attempt by taking inspiration from traditional Japanese wood joints. The metal connectors are replaced by a series of recesses and extrusions. The panels can now interlock using a single material which reduces complexity in the fabrication process.
In the version B the panels interlock only along the x plane. To rectify for this, version C was created. Here extrusions and recesses on all sides ensure interlocking on two plane and more stable wall.
Wall panel versions B,C
The final version of the panel design retains the same characteristics that ensure interlocking on two planes. I also contains a new element, a temporary reinforcement. It‘s purpose is to stabilize the wall in the cases where only one side of the wall needs to be removed, as when dealing with walls that divide housing units.
Two skirting boards assist with the attachment and need to be removed. The panels are then removed. As soon as the panel is removed, the temporary reinforcement becomes accessible. It can be lowered, reducing the risk of an unstable wall on the other side. The process is then repeated until all panels have been removed.
With this process, an interior wall can be disassembled and reassembled in a matter of minutes. Rooms can change function at any moment an for any length of time. In case of a renovation, only one side of the wall can be removed an replace with panels of a different style.
Wall panel final version
Exterior wall panel
IMPLEMENTATION
01 Building configuration
02 User input
Groups of people and families of any size, can decide to live together in a neighborhood. Each household is presented with a user interface. Through a four step process they can design their apartment and place it in the building.
1. The user chooses apartment size
2. The user can choose between flat floor and duplex. This influences the apartment size and the cost. The user then can start populating the apartment grid with the rooms in their preferred configuration.
3. The produced apartment is then placed in the pre-selected neighborhood. The system takes into account the designs of the whole group and produces a catalogue of possible position for them. By ranking the results of the catalogue, the group eventually reaches a consensus and the final placement is decided.
4. The interior partitions can be customized for each room.
03 Apartment configuration
Using Grasshopper and the Monoceros plugin, a process was developed for creating different apartment variations. Three models are extracted: a simplified that is used to fit all the apartments in the building, a full 3d for visualization and a graph that represents the spatial relationships.
In order to better utilize Monoceros, the room units are sliced to fit a 3,5 m x 3,5 m x 3,5 m cube. This means that the resulting geometry that is sent into the solver includes 1/4 of the actual columns and 1/2 of the beams and the walls. This is necessary in order to ensure that there will be a proper geometric continuity between the rooms of the final apartment.
Due to the limitations in the number of geometric elements that Monoceros can handle, it wasn’t possible for the full catalogue of walls to be used. Instead, four wall types are used, representing four different kinds of room-room interface:
Full wall: No communication between the rooms.
Door: Rooms are connected through a door.
Window: The room has visual contact with the exterior.
Empty: Rooms are creating a single, unified space.
Cell geometry slicing
Room types
Five different room types were recognized and they were allocated to the different room uses. Monoceros doesn’t rotate the input geometry. For this reason, by producing all rotation of the four walls, a list of all possible rooms was established. The rooms were then grouped by type and allocated to different uses, based on the table above.
Room rotations
Construction of rules of connection
Curves that are transformed into connection rules are drawn between opposing halves of the same wall interfaces. After a series of filtering operations the desired list of rules is constructed.
The apartment configuration process using Monoceros
04 Fitting
The building is broken down into three floor neighborhoods, each centered around a common public area. Groups of residents can come together and decide their preferred view, form the list produced during the building configuration.
Starting from the first floor, the closest cell to the view is selected and the shortest path between it and the core is plotted.
This main circulation path expands and forms a larger public space. The size of that space is determined by the number of residents in the neighborhood.
After it laying out 50% of the public space cells, the path grow vertically and creates the next to levels of the public space. Staircases are then added, and the cells that are free to accept housing units are selected.
Once the layout of the neighborhood is created, the residents can submit their apartment designs. These units are fitted around inside the neighborhood, using Wasp, a grasshopper plugin for discreet element design. Handles are created on the faces of the bathroom / entrance cells and a second set of handles are created on the units themselves. The locations of these handles is determined by the spatial relations of the units.
Through Wasp, a big catalog of solutions is produced. The solutions that do indeed contain all of the input apartments are isolated and given to the group of residents, who can decide on their desired configuration.
By repeating this process, the entire tower can be produced. The volume is split into neighborhoods, the circulation cells are extracted and each neighborhood‘s units are then fitted. The whole process is rule driven. Reserving parts of the tower for a specific function (eg fire escape staircase) is possible, by manipulating the Wasp rule set.
DESIGN PROPOSAL
All housing units can be easily reconfigured. In this example, the walls of the bedroom are disassembled. One of the CLT pieces is also removed. In the new space a staircase can be added. By expanding on a second floor the residents can add two new rooms to their house with minimal cost and disruption.
Infinite3 is a project of IAAC, Institute for Advanced Architecture of Catalonia developed in the Masters of Advanced Architecture 2020/21 by Students: Christos Trompoukis, Victoria Fedorova, Ziying Zeng and Iulia Maria Lichwar
Faculty: Areti Markopoulou, David Andrés León & Raimund Krenmüller
Faculty Assistant: Nikol Kirova