Digital Fabrication | Fall 2020 | MAEBB | Philipp Wienkämper
plyable | pliable plywood chair
plyable started with the question “how to make a comfortable and interactive plywood chair?”. Inspired by the possibilities of digital fabrication tools, I decided to use a technique to change the material properties from rigid to pliable. Therefore, I would use a technique called “living hinge” not only to archive the flexibility of the material but also as a focus for the Design. In addition, it was also important to keep the assembly simple with the least parts possible while still maintaining stability and respecting the dimensions of a lounge chair.
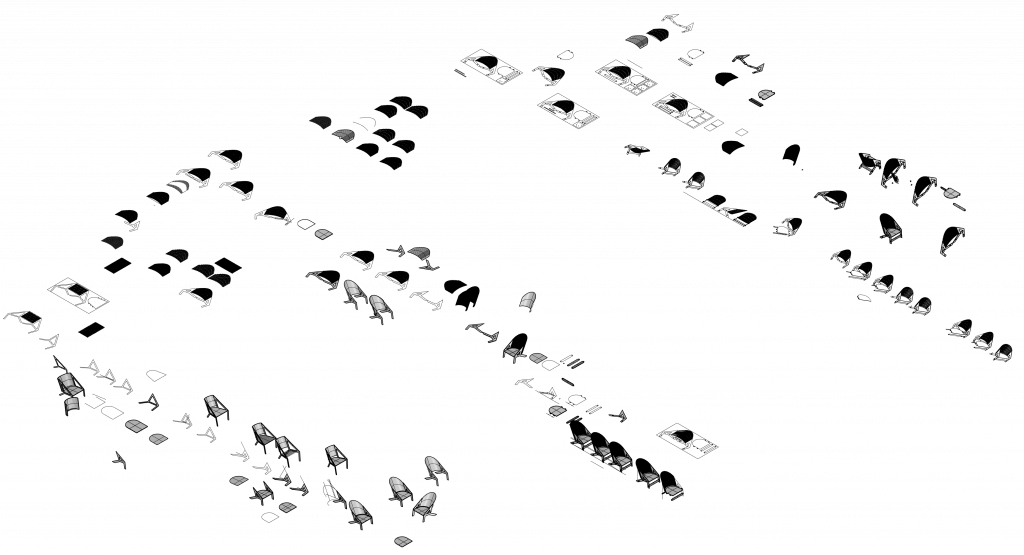
Design iterations
Prototype
The prototype was produced to test the flexibility and strength performance of the backrest-hinge and the connections of the separate parts. Therefore, I cut the prototype out of a 5mm plywood board with a laser cutter. The scale of this prototype is 1:3, which was important so the living hinge would have similar properties to the 1:1 model, which made from a 15mm plywood board.
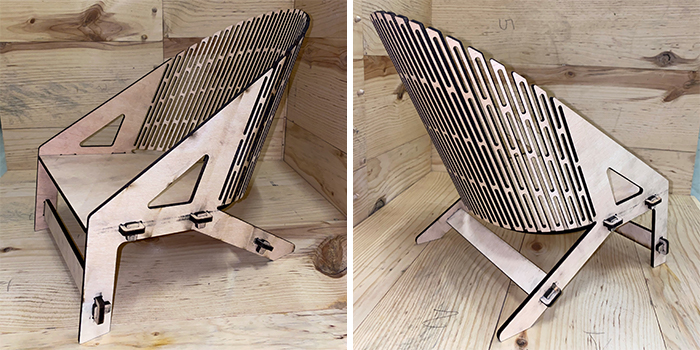
Prototype 1:3
Prototype stress-test
The stress-test of the “living hinge” was done to determine the potential weak points. Therefore, the load increased until the side connections of the backrest break. With these results, the thickness of the living hinge connection parts where adjusted to prevent the backrest from breaking.
Final Design

Elevations
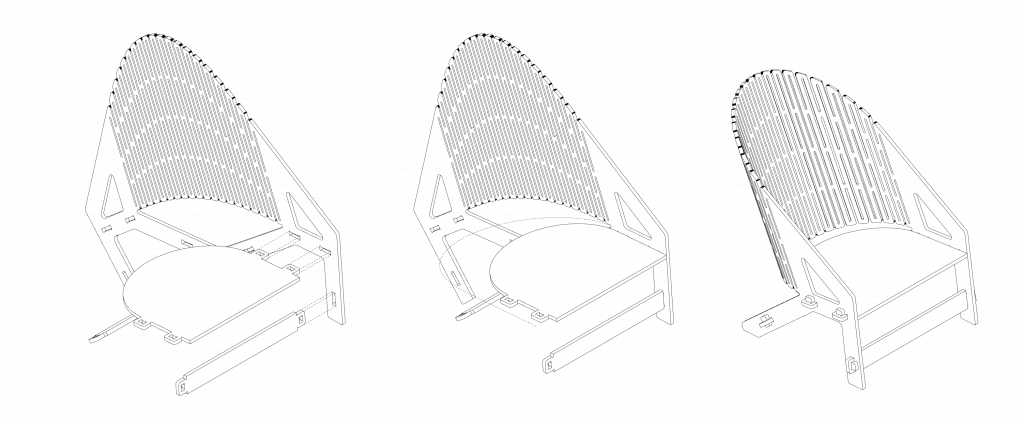
Assemlby
Fabrication
For the fabrication, all parts where cut out of a single 15mm 2440mm x 1220mm plywood board. Therefore, I used the CNC machine with a 6mm end mill. Finally, the four pieces will then joined by just using the CNC joinery instead of additional screws or glue.
Credits
plyable is a project of IAAC, Institute for Advanced Architecture of Catalonia developed at Master in Advanced Ecological Buildings and Biocities in 2020/21 by students: Philipp Wienkämper, and faculty: Eduardo Chamorro