The goal of this exploration was to use the robotic wire cutting process in order to perform cuts on clay extrusions and then aggregate them into a system that is able to manipulate the way air moves around and inside of it.
MANUAL EXPLORATION
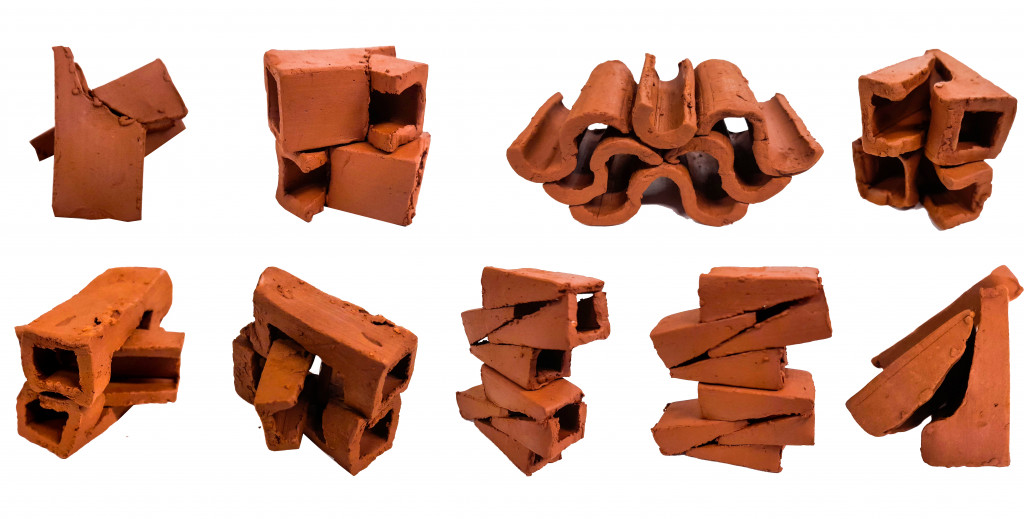
Manually exploration. Scale 1:3
For the manual exploration of the principles wire cutting process, 1/3 scaled models of the final clay extrusions. As a starting point for the manual exploration, two simple principles were used. To perform one single cut and to use both parts generated. The goal was to achieve complex geometries in the final system, by starting from a simple cut. Both parts are used to eliminate material waste. This principle has a big impact on the design of the final geometry.
DIGITAL EXPLORATION
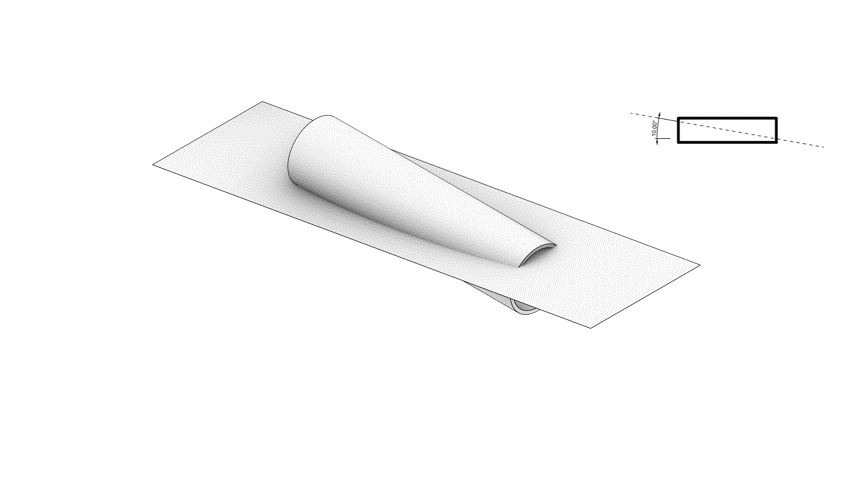
Single cut exploration
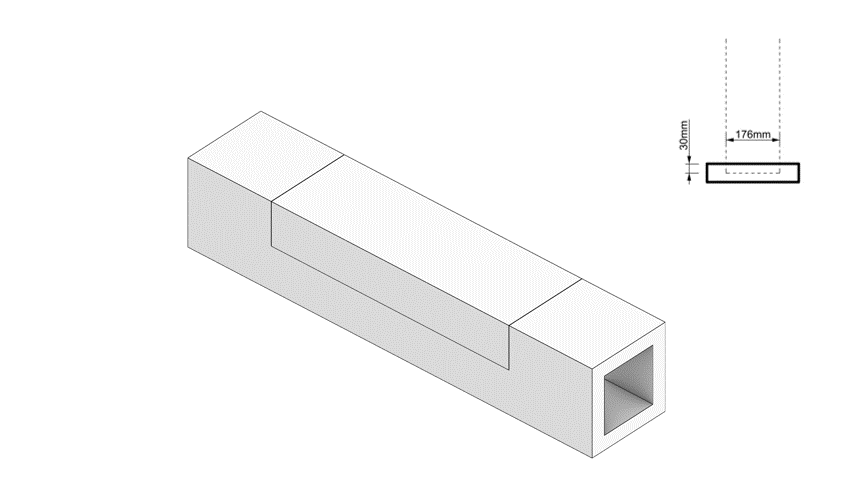
Straight cut exploration
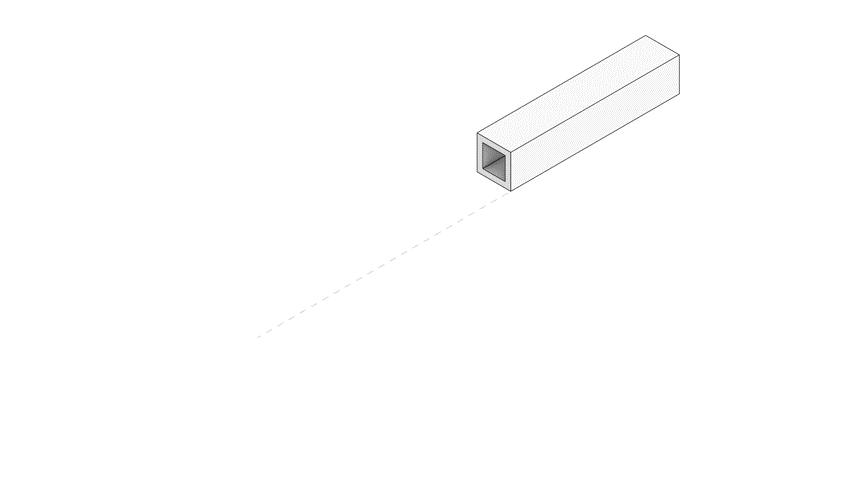
Circular cut exploration
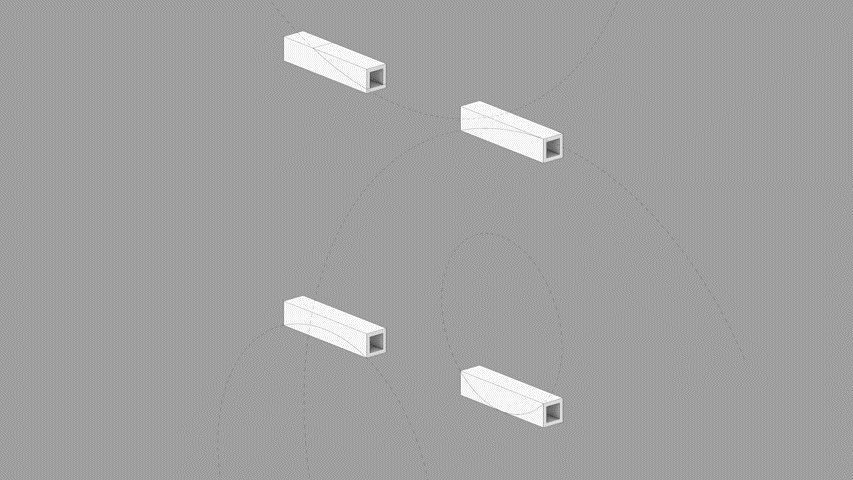
Analysis of the possibilities of combining the pieces generated from circular cuts
During the first steps of the digital exploration three cuts were created. The linear cut allows the creation of two identical parts that can be connected in various ways . The rectangular cut allows the small part generated to fit inside of the bigger ones. The circular cut allows the rotation between the two generated pieces.
AGGREGATION EXPLORATION
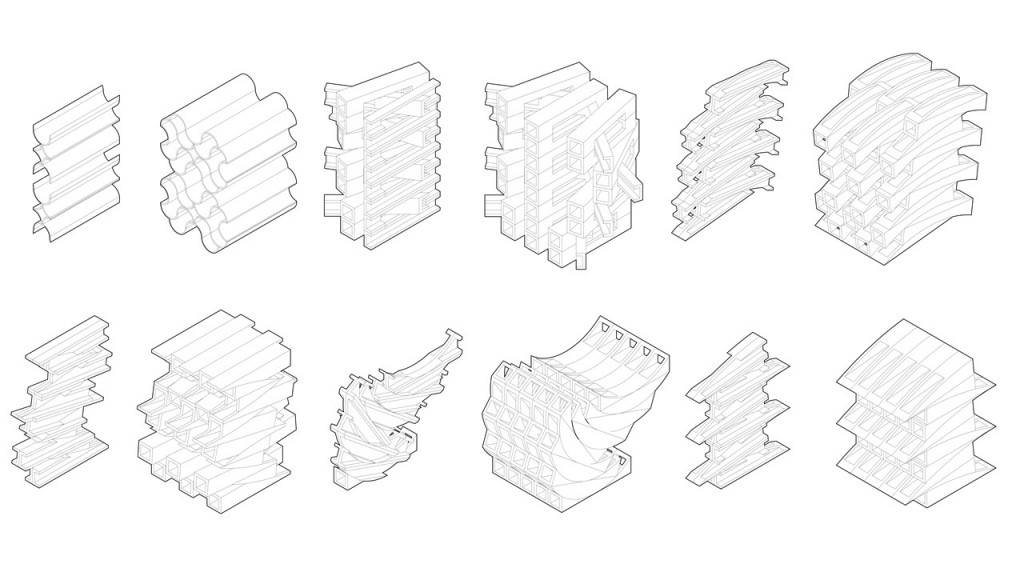
Formal exploration of aggregation and analysis of the resulting interior.
The circular cut was selected for the final design. Many different circular cuts were created during the exploration for a ”smart” facade that controls the amount of air that passes through it. The cut that was selected allows to flip and rotate the two parts generated. The angle of the rotation controls the back opening of the final unit.
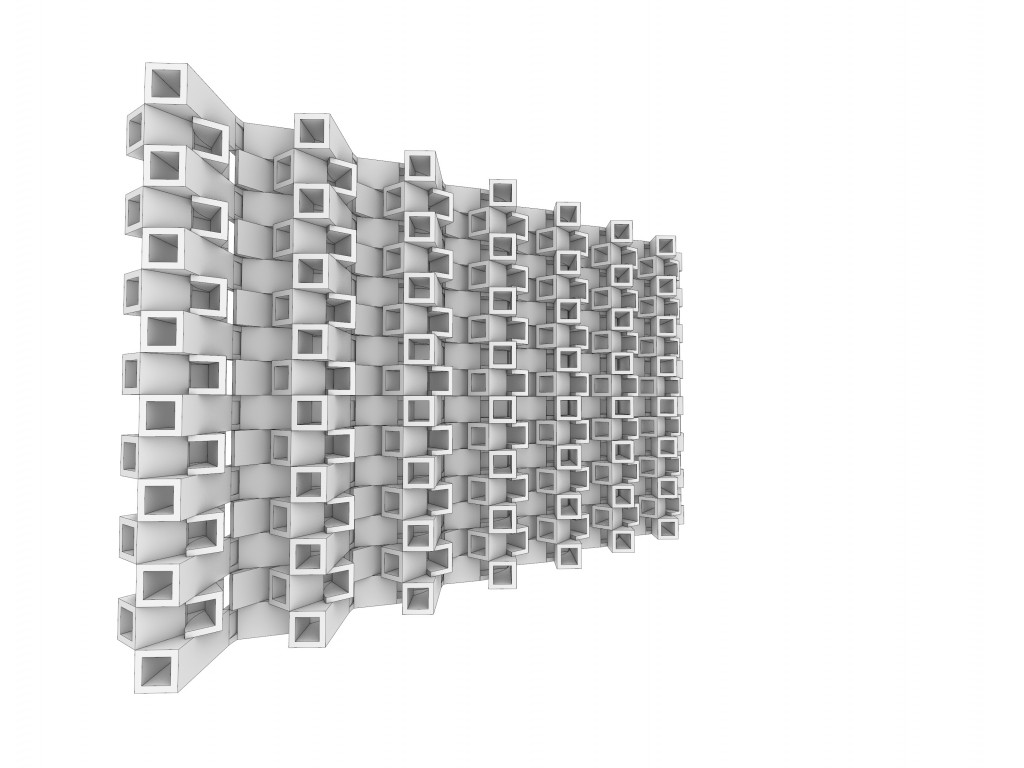
Architectural composition
FINAL AGGREGATION
One of the goals was to use and even enhance the properties of the material. Clay becomes really rigid after it dries and allows the stacking procedure to happen without the use of any supportive material. The final geometry acts as a wind catcher and controls the amount of air that passes through it.
ROBOTIC WIRE CUTTING PROCESS
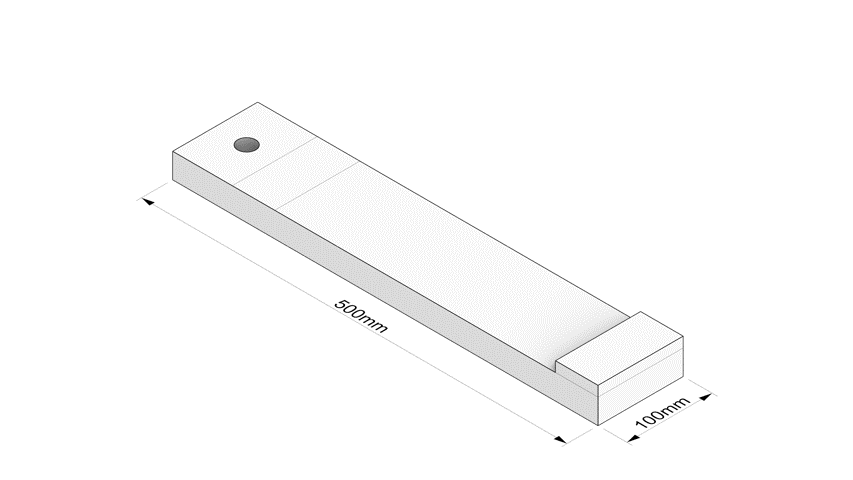
Production process
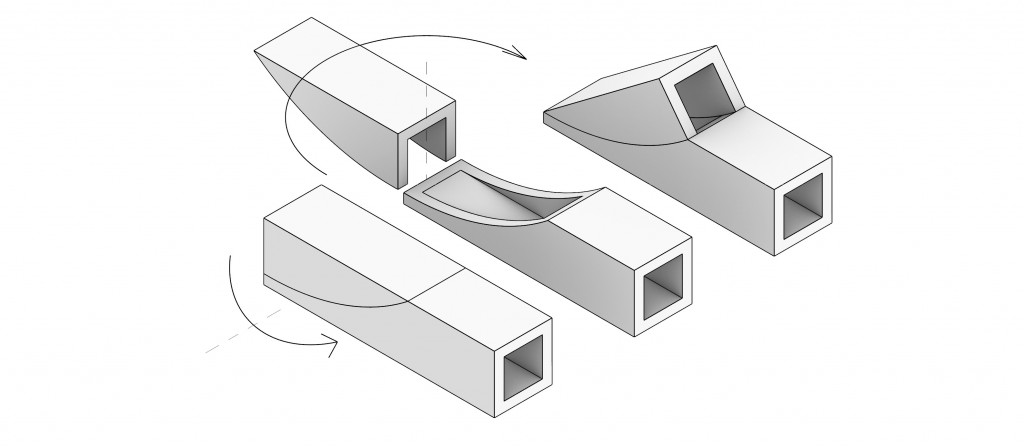
Support for the process of cutting and rotating the pieces to define the type of aggregation
For the cutting process a base was created to assure the stability of the clay extrusion. The base is fixed to the table and the robot pushes against it, allowing a clean cut.
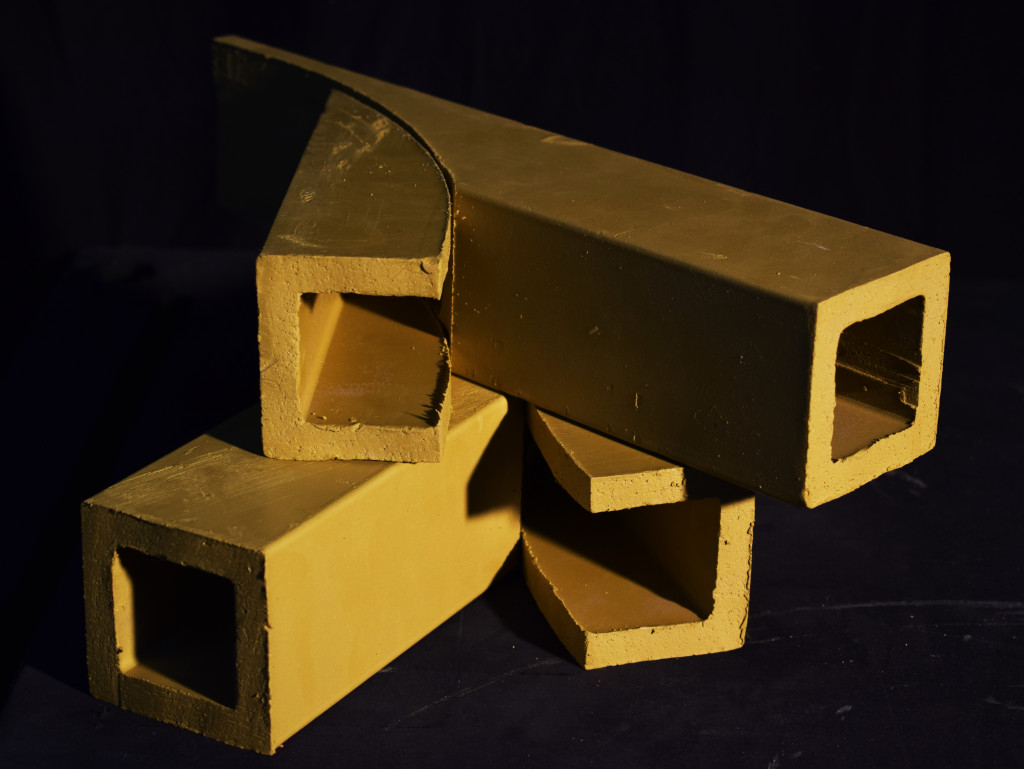
Final prototype
CFD ANALYSIS
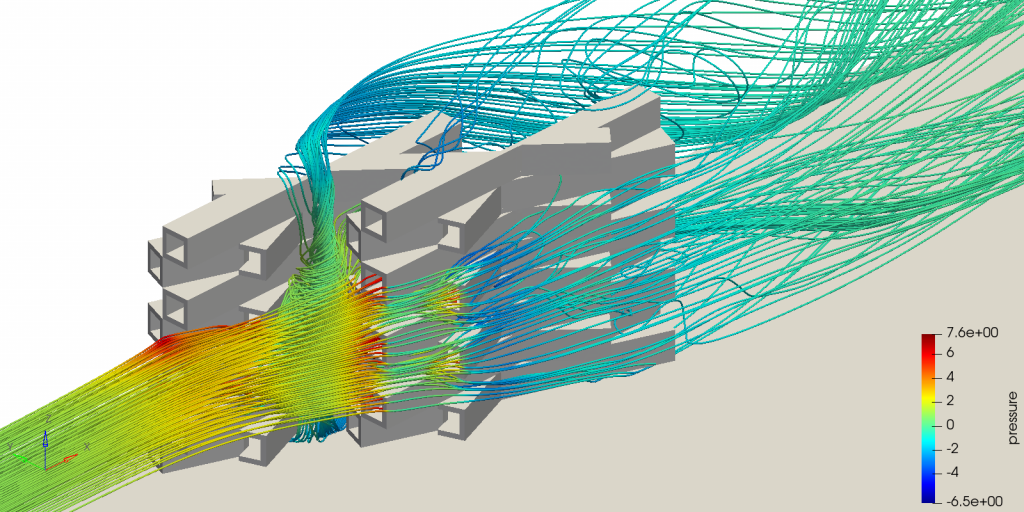
CFD Simulation
At first a diagram of the expected behaviour of the air through the system was created.Then the CFD analysis of the air flow was created using the provided software from Altair/Hyper works. From the analysis it is clear that there is some turbulence generated in some parts of the facade, which could be a topic of further exploration about how to avoid this phenomena. Air flow simulation analysis is a back and forth procedure that informed the designing process and allowed some feedback without having to perform physical experiments with the system.
Single Cut | Multiple combinations of clay parts is a project of IAAC, Institute for Advanced Architecture of Catalonia developed at Master in Robotics and Advanced Construction Workshop 1.1 in 2020/2021 by:
Students: Alberto Browne, Juan E. Ojeda, Orestis Pavlidis
Faculty: Kunaljit Chadha
Faculty Assistants: Anna Batallé Garcia, Soroush Garivani, Ashkan Forughi Dehnavi
In collaboration with: Toni Cumella / Ceramica Cumella
Supported by: Ant Studio, Altair
Workshop Participants: Shahar Abelson, Hendrik Benz, Alberto Browne, Charng Shin Chen, Michael DiCarlo, Helena Homsi, Arpan Mathe, Juan E. Ojeda, Orestis Pavlidis, Aslinur Taskin, Alexandra Timageni