Deployable Space Frames >>A Proposal to Reuse Scrap Profile in Temporary Public Structure That utilizes Robotic Assembly Manufacturing
Design Hypothesis
The purpose of this project is to develop a design and production process to create Deployable space frames by reusing a variety of pipes that would be considered as construction industry waste.
The main subjects that were developed are:
– Material Harvest – A strategy for all stages of the pipes management.
– Connector – The design of a part that allows the connection of the pipes to create bigger foldable aggregations.
– Production Informs Design – The procedure of in which small assemblies are produced flat robotically, and unfolded on deployment.
–Pipe, Assembly, Structure – A design Strategy that is based on a set of simple assembly typologies that will be aggregated into a structure.
Material Harvest >>PIPE MANAGEMENT
The construction industry is producing a lot of waste and a big part of it is pipes and rebars used in various parts of a building. The first step of the project is to identify and collect a variety of used pipes of different material, diameter, length and color. After the material is collected, we identify the parts that are still functional and thus useful for us and, cut and remove the rest. Then the parts are stored according to material, geometrical and aesthetic properties.
CONNECTOR
Designing the connection method posed the project’s main concern. During this exploration several strategies were tested following three fundamental rules:
– Providing three degrees of freedom.
– Allowing a flat assembly and unfolding.
– Providing tolerance during the robotic assembly.
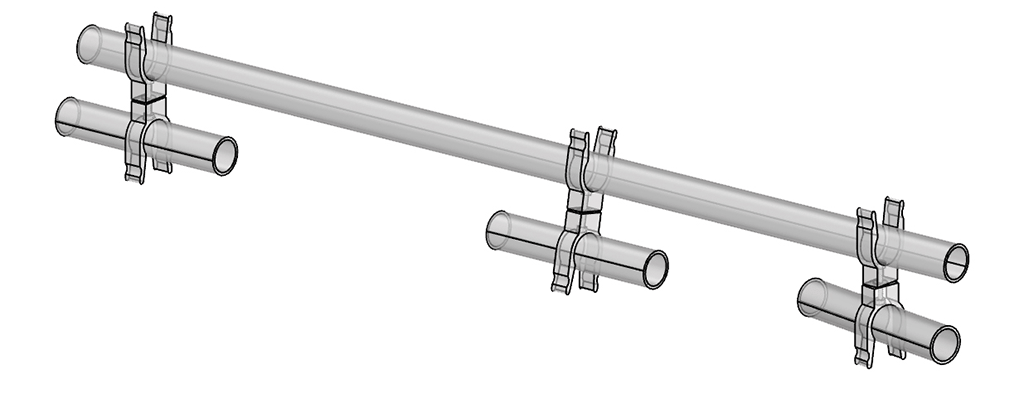
Connector’s Translation and Rotation
As the system is using pipes of various dimensions, the final design for the connector is a “universal” version that can receive a variety of dimensions. During the exploration HDPE material was used because of its flexibility that helps in the robotic assembly process. In the future development of the system, other more rigid materials like solid Aluminum could be preferred.
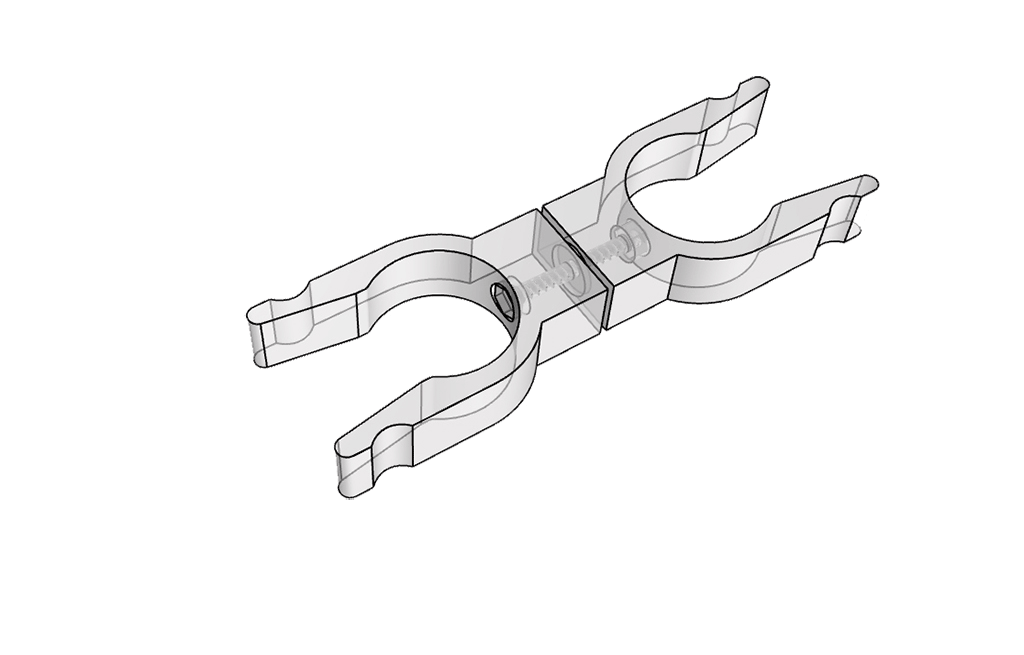
Connector Assembly
Production Informs Design – Foldable Sub Assemblies
Early robotic testing laid one of the main project’s design paradigm – Flat Assemblies as a way to decrease Robotic assemblies uncertainties. Theses Assemblies will be robotically manufactured – this reducing labour intense tasks, will keeping the ability to mass customize each assembly. After the parts of the system are designed the challenge of designing with it arises. The strategy that was used is to design small foldable aggregations-typologies that can be combined and assembled into the final spaceframe. Each typology contains aggregations of different proportions. In the future workflow the procedure would be flipped. A tool would design the whole space frame and divide it into smaller foldable aggregation.
Pipe, Assembly, Structure>>design Tools and large scale implementation
due to the dynamic nature of this system – Structural generative tool and analysis are required. In this example topology optimization and FEM was to specify the final design followed by populating the stretched a tetrahedron – one of the developed typologies. The Transition between the the topology optimization, FEM and populating are meant to be iterative. Each stage adjusts the design and informs the next stage until a satisfactory convergence is reached. The intended usage we prospect to this system is of temporary structures such as festival, exhibitions etc.
-
Starting Point: Volume Loads and supports are inserted to the system
-
LOOP - stage1 :Topological optimization informs on the design space needed
-
LOOP - stage2 :The FEM informs on the structural properties each cell needs to withstand.
-
LOOP - stage3 :The geometrical Populating locate and place pipes from the stock and changes the design according to the available parts.
ROBOTIC ASSEMBLY
As the robotic assembly was part of the course’s deliverables, it affected every step of the designing process. The units are assembled folded flat, packed and transferred to place there the
unfolding and connection between them is happening. As a part of the research a gripper that can receive both the pipes and connectors was designed. As a positive feedback from many tries using different robots, the way the system is designed allows for a lot of tolerance during the assembly and even corrects itself in some cases. The experiments that were performed are
- 1/3 scaled model using the ABB 120 robotic arm and in
- 2.1/1 model using the KUKA KR150-240 -2 L110/180 robotic arm.
</p>
</p>
FUTURE WORKFLOW
Future spats of the research and development of the system would be:
Further explore the collecting process of the pipes and doing research on the waste that The construction industry is creating.
Consider different material for the connector.
Invent a designing tool that will help us gain more control of the system.
Completely automate the robotic assembly process by using collaborating robots, one for bringing the material from the store and one performing the assembly.
</p>
Deployable Space Frame is a project of IaaC, Institute for Advanced Architecture of Catalonia developed at the Master of Robotics and Advanced Construction program in 2020/21 by:
Students: Shahar Abelson, Orestis Pavlidis
Faculty: Alexandre Dubor, Raimund Krenmueller
Faculty Assistant: Roberto Vargas