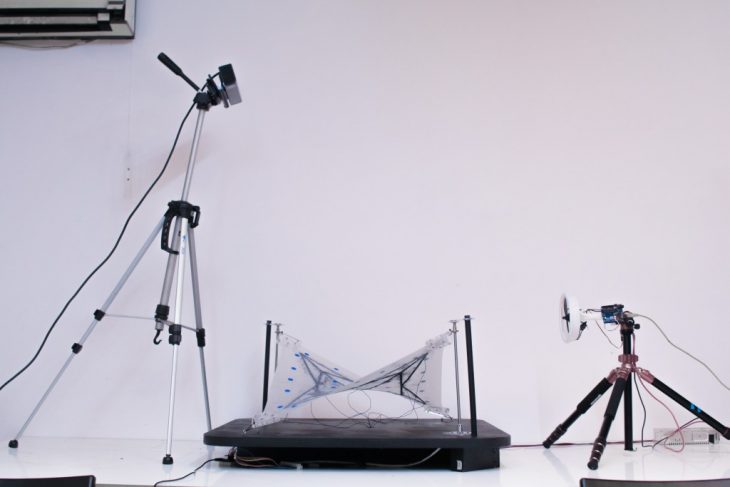
Digital Matter – Alive – Learning set-up
The following research explores possibilities of graphene material systems enhanced with artificial intelligence algorithms in context of smart architectural membrane elements addressing performable augmentation of structural and environmental behavior, in particular focusing on scenarios involving wind actuation.
Keywords: responsive architecture, material intelligence, buildings that think, adaptive structures, artificial intelligence, digital fabrication, graphene, material system, membrane, sensing, adaptation
Membrane Introduction
Our research followed a bottom up approach wherein we started from exploring material properties and proceeded by maximizing utilization of them in a architecture related scenarios. Graphene has been know as a theoretical material for a long time and it’s chemical properties very predicted more or less accurately. Essentially it is a single atom layer hexagonal lattice of Carbone. However, it’s relatively recent fabrication uncovered unexpected range of physical properties that opened up possibilities for unique applications. Thus one of the most promising and broad characteristics is it’s electrical conductivity.
As with any conductive material the relationship between deformation and current is upon certain level of abstraction of the model – linear. Thus by applying specific types and sequences of deformation you would get a unique correlation. By initially feeding the shape and conductivity of the planar extension of such element through AI algorithms you can train a surface to avoid complicated shape feedback steps and infer shape only by knowing conductivity through the surface.
Examples of surface being trained for single point pressure scenarios and its response behavior:

Digital Matter – Alive – Training Single-point Pressure
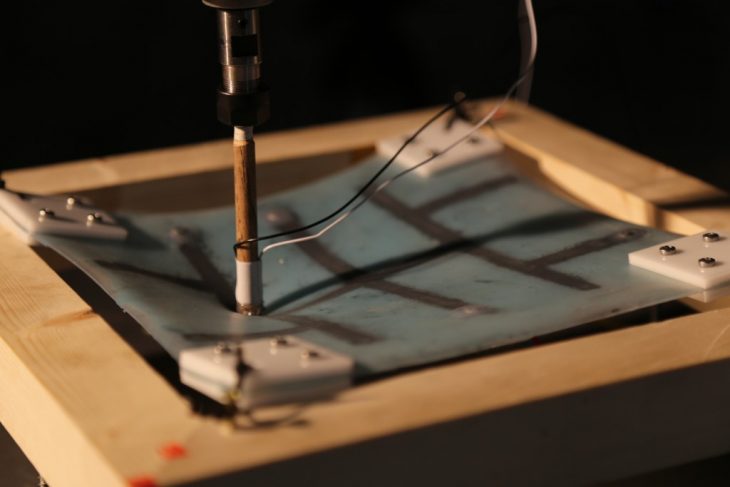
Digital Matter – Alive – Training Single-point Pressure – 2
Results:
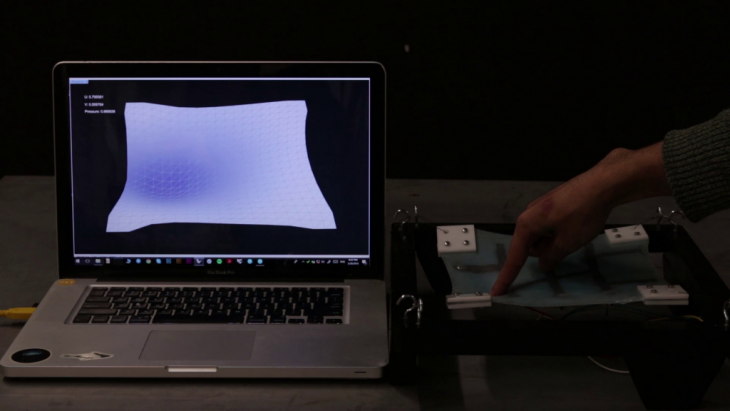
Digital Mater – Alive – Single Point Pressure Prediction Performance
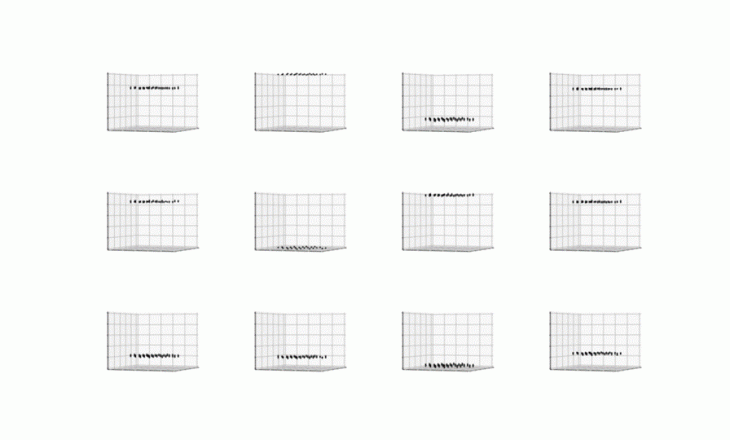
Digital Matter – Alive – Data Visualization
Taking this concept one step further, in every scenario certain parts of the membrane would contribute differently and the surface has to reflect it. Thus with rather accurate electrical circuit simulations, and physical simulation of the surface behavior the pattern we optimized to be universally sensitive but uniquely identifiable.

Digital Matter – Alive – Circuit Simulation
Membrane fabrication:
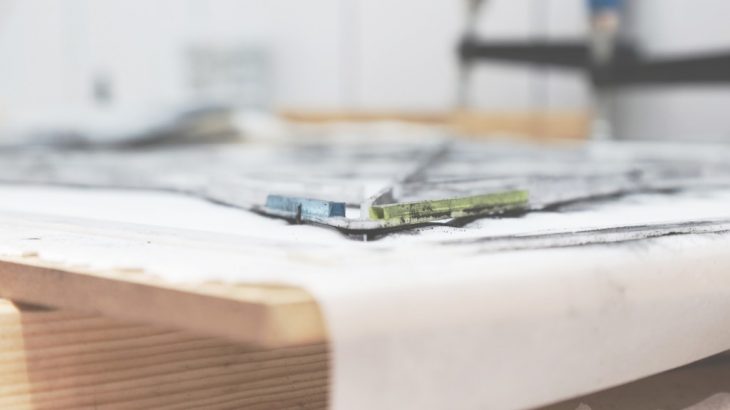
Digital Matter – Alive – Membrane Fabrication Close-up
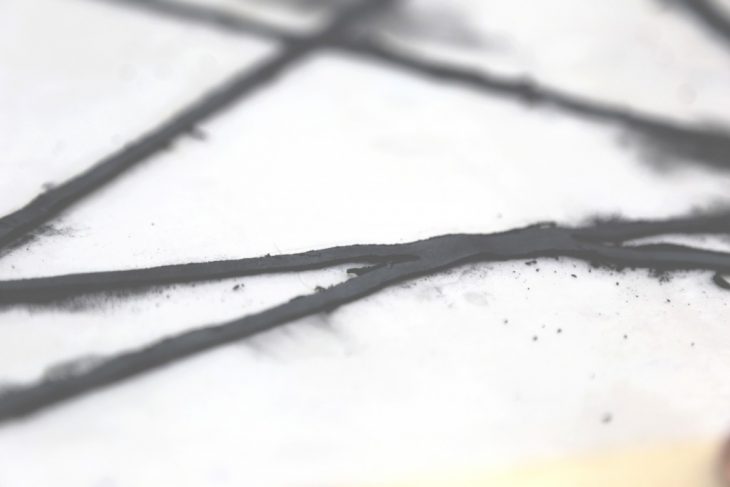
Digital Matter – Alive – Membrane Close-up
Prototype and its behavior:
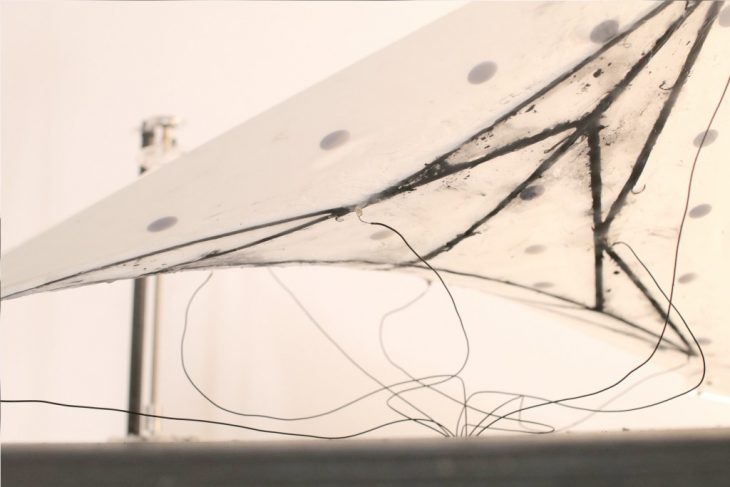
Digital Matter – Alive – Prototype close-up
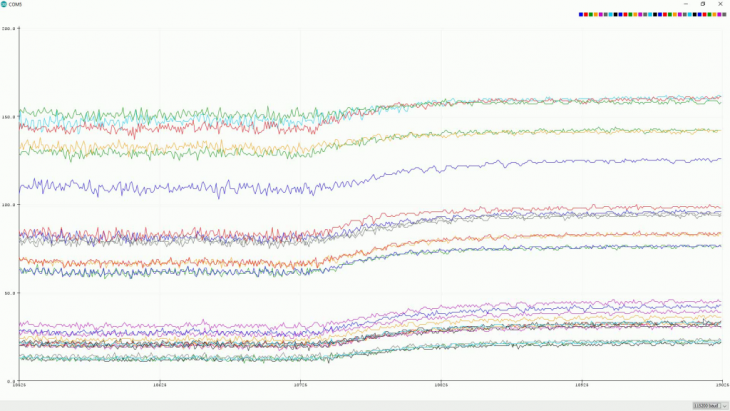
Digital Matter – Alive – Wind Effect on the Surface
Vision
We live in an extremely interconnected world. Indeed, everyone is almost instantaneously accessible and any two places are almost momentarily linkable. However, our physical environments have been slow on adapting to this spatial paradigm shift. We don’t normally see interactive materials, dynamic structures and intelligence embedded to the material itself delegating reactivity and performance to it. By way of contrast, our fabrication technologies though already allow us to exit mass production era to more tailored and more controllable systems and environments.

Digital Matter – Alive – Membrane deformations
For this reason, this research tries to address this emerging niche and propose and membrane that not only classically behaves as a separator but has equally present intelligence to it. On one hand, we want our buildings to be interactive, ALIVE having autonomy to a certain degree. On the other, we cannot exclude user from the ecosystem. Our vision that this, and possibly other, smart material systems could fill our urban and local spaces. A distributed network creating an interconnected system of sensors, information sources and actuators. It could not only gather big data but allow more dynamic interaction between us and the spaces we live in.
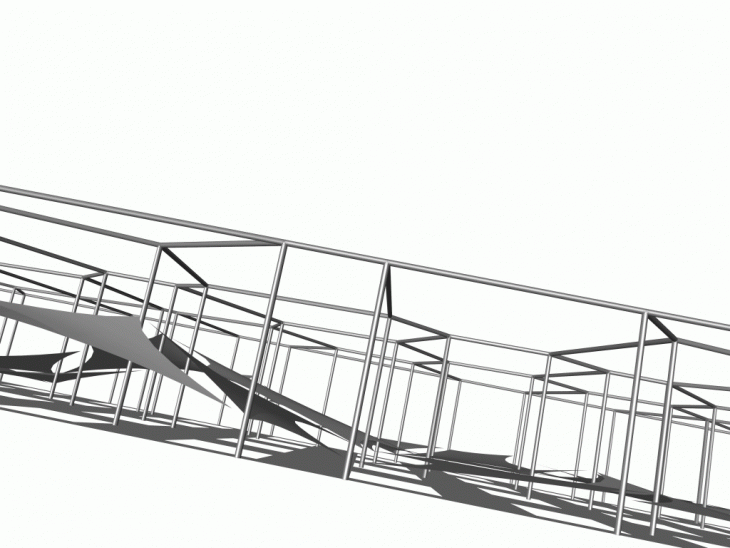
Digital Matter – Alive – Application Animation Example
applications
If the building was to be covered in the skin that could understand local wind flows and adjust it’s shape to reflect it, channel it or locally let it enter the protected space with an opening.
What if the high wind scenarios of sails and tents – dramatically oposite (maximizing and minimizing influence of the wind) but ultimately requiring same information could adjust themselves in order to maximize certain geometrical goal and not abstract physical units.
Not only this but, what if the user could wear fabrics that understood the gestures and patterns of movement in order to link physical movement with digital layers of the space. In fact, we already introduce heavily with AR and VR technologies that drastically change the use of the spaces. Furthermore, the dynamic inner space separators could understand the touch and the pressures they are subjected to. By informing the user of needed adjustment we can further enhance the digital-physical linkage.
These examples are just a few that this material system allows to introduce.
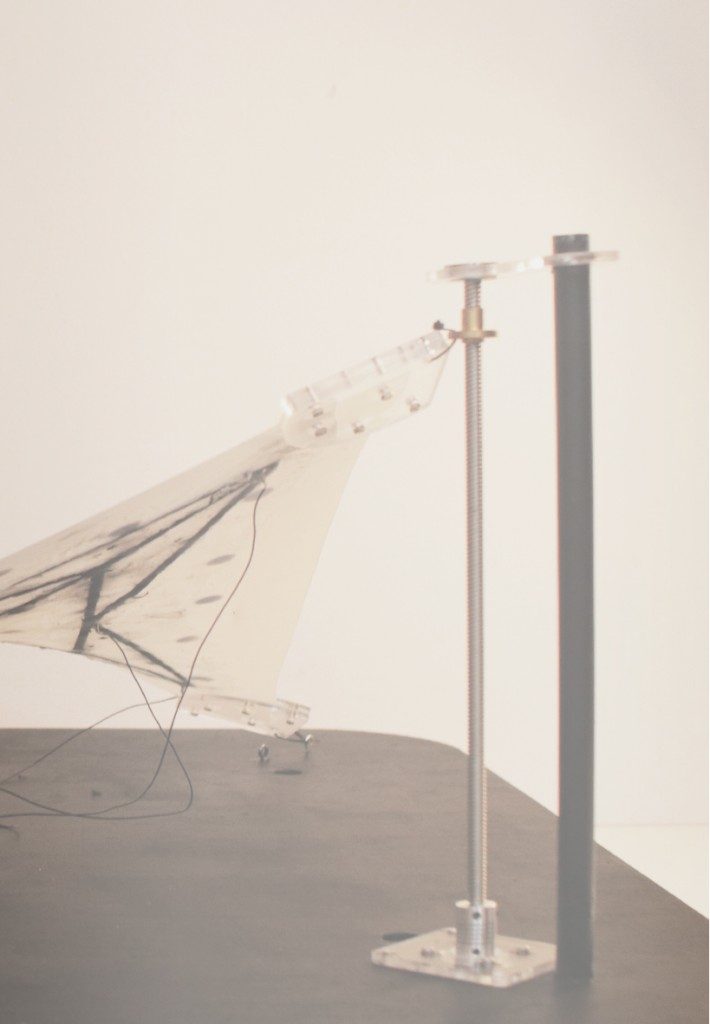
Digital Matter – Alive – Prototype
—
IAAC // MAA 01 // RS.3 Research Studio: DIGITAL MATTER
Researchers: Ardeshir Talaei, Soroush Garivani, Daniil Koshelyuk
Lead Faculty: Areti Markopoulou
Faculty Assistants: David Andrés León, Raimund Krenmüller
Computational Advisor: Angelos Chronis
In collaboration with: IIT, the Italian Institute of Technology and the Smart Materials Group
IT Material Experts: Athanassia Athanassiou, Ilker Bayer, Giovanni Perotto, Material Scientist