Infestation & symbiosis of deep sea creatures in humans of the future
Human activity is having a devastating effect on oxygen levels in the world’s oceans, and could cause parts of the Pacific Ocean to essentially suffocate in as little as 15 years. Warming ocean waters can’t hold as much oxygen as colder water, and researchers at the National Center for Atmospheric Research say de-oxygenation of the ocean’s warmer upper layers will disrupt marine ecosystems in a big way. Studies have recently found an increase in a microorganism known as phytoplankton. These organisms are responsible for generating oxygen by means of photosynthesis and carrying it to the deep sea, but warmer water means less oxygen and less mixing of ocean layers. This causes a problem as the other ocean organisms living deep below the ocean’s surface may not be able to survive if less oxygen is being brought down. The effects of global warming could dramatically upset the ocean’s natural systems.
</p>
?
Future predictions
??We imagine a future that is completely dark. Where humans have evolved into an altered state of organisms, forming a different species interdependent on each other. Humans have had a devastating effect on oxygen levels in the ocean resulting in a inhospitable environment for deep sea creature. They can not survive in the depleted oxygen water anymore and, therefore, retaliated against humans, infested human bodies in order to survive.
The human race has undergone a paradigm shift, engaged in a symbiotic relationship with other organisms. These organisms grow out from the spinal cord as the human sensory receptors are located in the head and are able to release a light by means of a chemical reaction that the new organisms produce.
Organ
?Our concept for the skin was to create a new organ as an extension of the human body. We want to host living organisms on our second skin to illuminate the otherwise invisible creatures from the deep sea. Due to scarcity of oxygen resources in the future we are addressing the new territories where organisms can live in more oxygen responsive skins. The human sensory receptors are located in the head with the spinal cord connecting with the body. The spine is rigid but flexible and is therefore ideal for integrating it as an application within the skin to contextualize the ‘organ’ with the body.
Experimentation and Fabrication
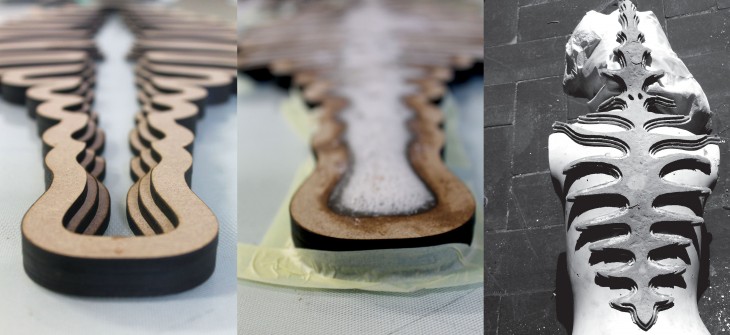
Casting and drying bioplastic form
We dried the bio-plastic cast on a mannequin in order for it to take the contour of the body and spine.
Drying in sunlight helps speed up the dehydration process, which also assists in deterring bacterial & fungal growth.
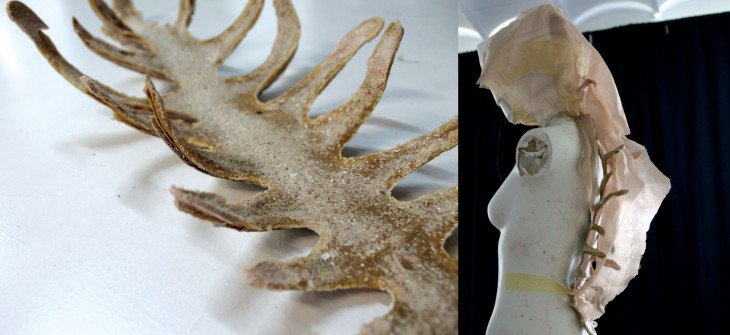
Draping with fabric over mannequin
The geometry of this wearable was developed from the handsketches, and then translated into a 3D model using Rhino. By modelling the design digitally it allows us to adapt the form to suit the human body proportions and scale. The 3D model of the body was generated using a software called: MakeHuman. The bio-plastic is prepared by cooking the ingredients together into a liquid solution. In order to contain and fabricate the bio-plastic we created an open mould to pour the plastic into. The mould was created from the flattened geometry to the 3D model, which was then laser cut. It is made using 3 layers of 5mm Medium Density Fiberboard, which were taped down to a flat glass casting surface. The glass was sprayed with olive oil, and the interior of the mould was smeared with Vaseline to act as a release agent for the cast. We added some fluorescent powder on the casting surface. The molten mixture is cast when it is above 25 degrees Celsius, otherwise surface tension in the material forms. Then the cast is left to dry overnight in a well-ventilated area. Once the cast has begun to dehydrate and harden, it can be gently cut out of the mould. At this stage the cast should feel somewhat soft and flexible like a gel, which was placed on the mannequin to take the contour of the back. And transferred to dry in the sun. As the bio-plastic ribs hardened they adhered more to the mannequin, which was an unpredictable result. In our previous experience working with bio-plastic, it usually shrinks and curls towards the side that is exposed to air. Also when there is a food waste content, the mixture tends to be drier on that side, which would also suggest that the dry side would curl first. The bio-plastic reduces in volume and size during the dehydration process. Therefore the mould was slightly oversized. Due to the unpredictable results during the drying process, we had to modify the assembly of the prototype. However part of the beauty of working with natural materials is that they contribute to their own formation in an organic way. This was a conscious choice on our behalf as designers in our material selection.
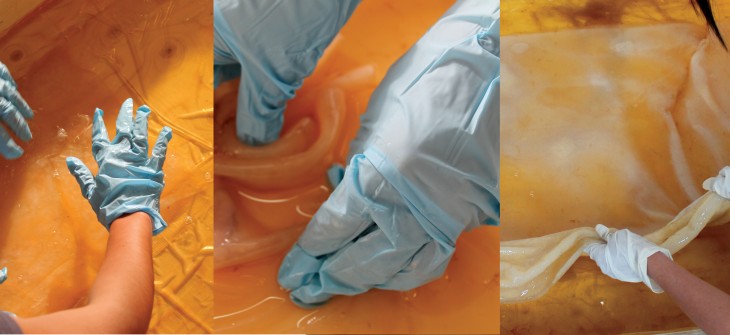
Kombucha growth
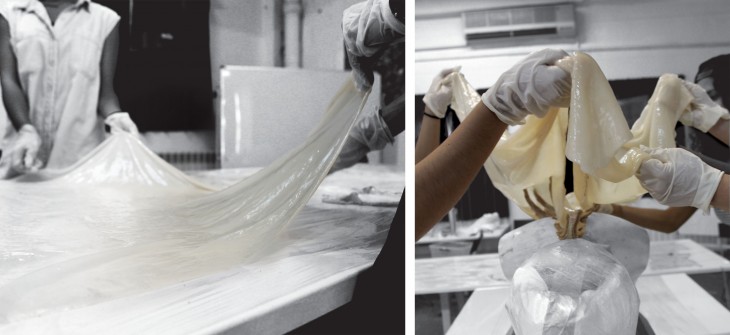
Draping Kombucha skin on mannequin
We harvested the Kombucha ‘Skin’ from the tank it had been growing in when it had reached 1cm in thckness. Ideally we could have waited until it had reached 2cm, however we were
limited by the amount of time required to dry it. In order to dry it we removed the layer formed by growing culture from the from the growth medium, and drained off the excess liquid. The bio-couture was then thoroughly rinsed under cold water to remove any debris. At this stage the bio-couture was quite heavy due to the large water content, and also prone to tearing. So, it was transferred to a flat surface to be rinsed. The growth medium tank was approximately 1 x 1m, so the SCOBY film reached the extents of this area. However we had originally started with a couple smaller rectangular samples, from different Kombucha cultures. In the process transferring and rinsing the material the layers from the various samples separated from each other.
After the samples were cleaned, we laid them out on a flat surface to flatten out any wrinkles in the material and also to determine which piece was most suitable for the prototype.
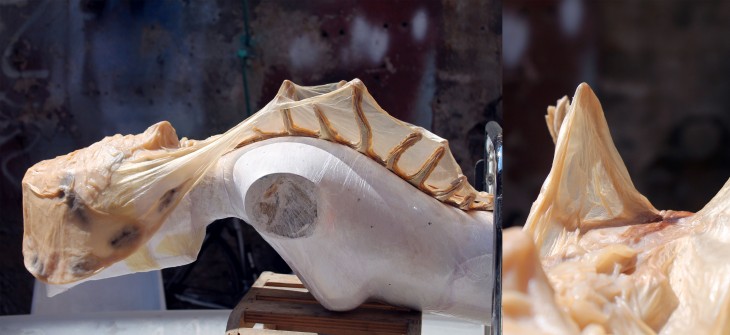
Skin drying in the sun
For our Skins2 prototype we chose the largest and most uniform material piece to drape over the mannequin and bio-plastic ribs. There are 2 methods of working with the bio-couture;
creating a seamless piece by working with the wet material or drying first, then sewing the material together conventionally. We wanted to experiment with draping and molding the
wet material and fusing the layers together. By directly draping the wet bio-couture over our mannequin, it would take the shape and dry this way. Once the bio-plastic was positioned, we
cut off the excess material using a scissors. It was relatively easy to cut through. To add more articulation to the design of the hood, we layered several smaller samples of
bio-couture over the main piece. Then we crumpled the material to emulate ripples in the flesh. The outer edges were folded to create a stronger edge seam. Since the wet material was
quite slippery, we secured it in place using metal pins. However we came back the following day to discover that where the metal had been in contact with the bio-couture there was a
dark discoloration. The assembled prototype was then laid out to dry again in the sun to speed up the drying time. The dry bio-couture is much thinner and more transparent than
when it is wet. It is also more brittle, so it must be handled with care.
IAAC, Skin2.
BIO[lum] SKIN is a project of IaaC, Institute for Advanced Architecture of Catalonia developed at Master in Advanced Architecture, MAA01 in 2016 by:
Faculty:
Manuel Kretzer
Anastasia Pistofidou
Students:
Thora H. Arnardottir
Noor Elgewely
Jessica Dias
Ingried Ramirez