Research Background
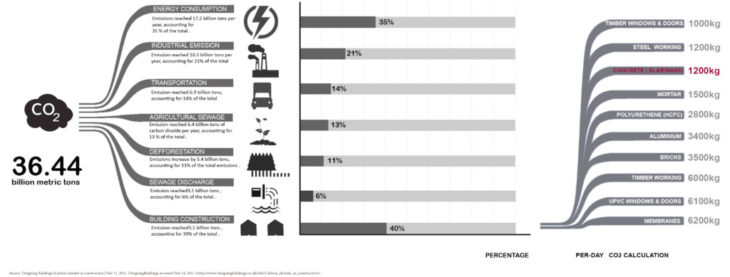
CO2 Emission Situation
The carbon dioxide released by people currently is huge every year: 36.44 billion tons of carbon dioxide is released per year, in which, 40% of carbon dioxide emission per year is resulted by building construction and 1200 kg of carbon dioxide is produced by concrete fabrication per day.
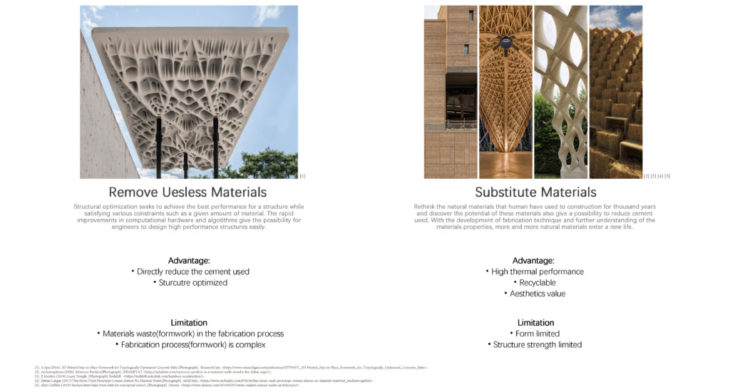
Method to Reduce Cement Used
In order to reduce the CO2 emission, people try a lot of way to reduce the usage of cement: either to use algorithm to find out and remove the less structure performance material, or to use substitute construction materials. However, limited by the materials’ properties and fabrication technique, people realized that concrete is still the best materials for structure from both construction side and structure performance side.
So, removing the less structural performance material becomes a sought-after topic in current architecture design field. People try to develop a mature fabrication system for the topological optimized geometries. But, with current technique, to fabricate such geometries will generate a huge waste in fabricating the formworks for casting.
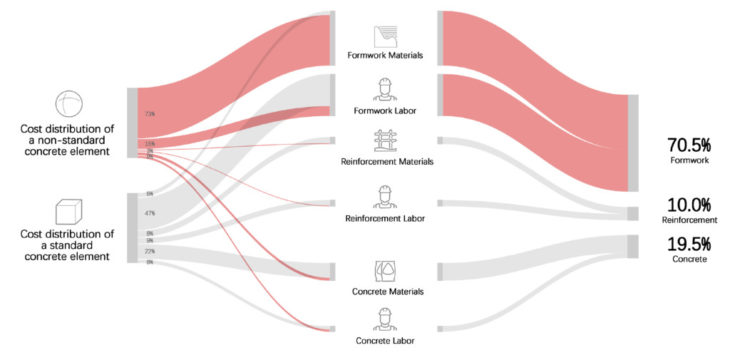
Formwork Cost for Concrete Casting
To further understand how formwork fabrication impact the whole concrete fabrication industries, research from Delft University of Technology shows that no matter for the standard elements or the non-standard elements, formworks respond to more than 70% of the entire cost.
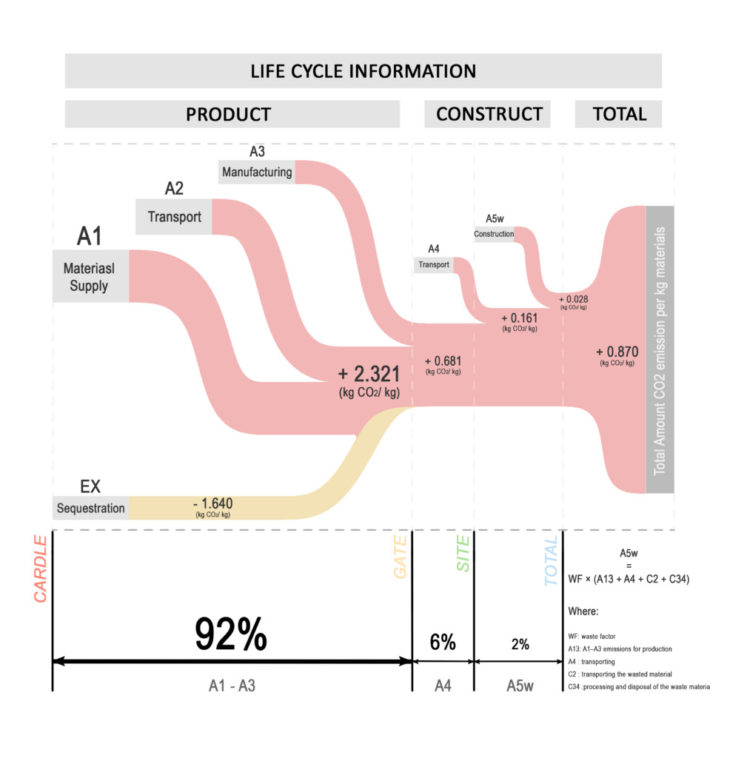
Embodied carbon of Formwork
When we zoom in to the embodied carbon of traditional plywood formworks: Assume 1 ton plywood formwork are produced and transported to the site with total 200km travelled by road. The embodied carbon of the materials will be 870kg.
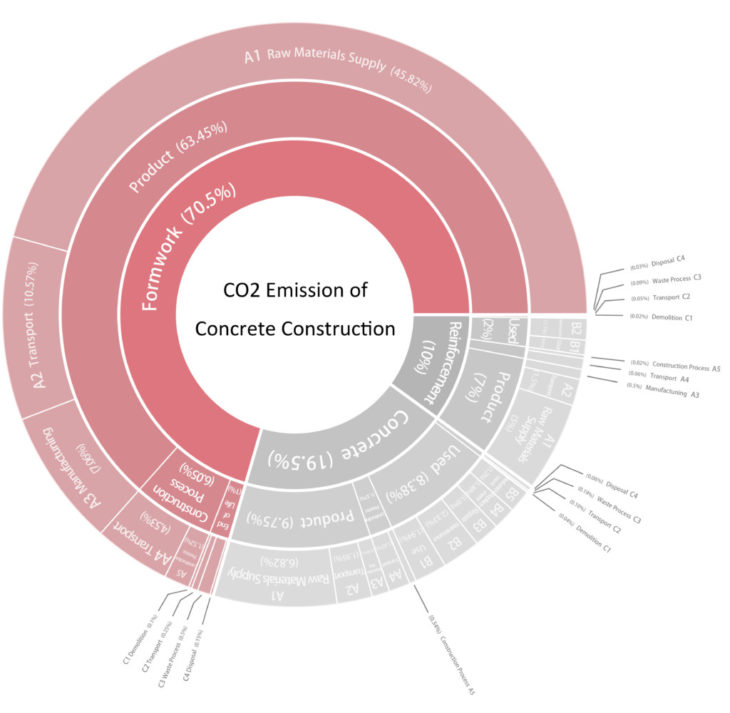
CO2 Emission of Casting
After the calculation of different perspective and we zoom out to the whole picture, a severe truth shows to us: formwork fabrication takes responsibility to 70% of CO2 emission in the while concrete industry, and 63.45% of CO2 emission is generated in product stage. Since most of the formworks could only be reused for 5-8 times and after the production life circle, them couldn’t be fully recycled, it’s a huge waste in using current way to cast concrete.
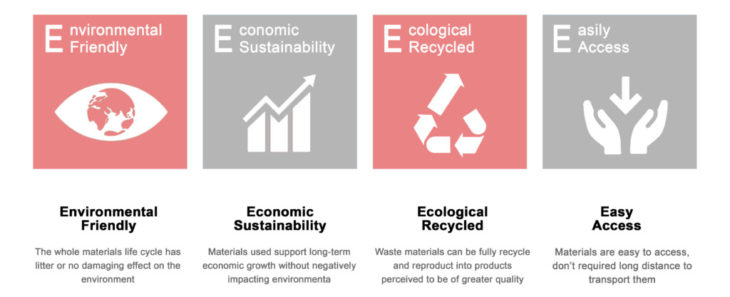
Main Aim
To achieve the 4E main aim: environmentally friendly, economic sustainability, ecological recycled and easily access, a question is thrown out: Whether there is a material with low environmental impact, low cost, and easily accessible that can be used as a formwork to fabricate castable materials with less geometry limitation?
To find out the potential opportunities of developing a new fabrication technique for castable materials. I take concrete as an example, study and conclude the advantages and disadvantages of current fabrication technique and formwork martials.
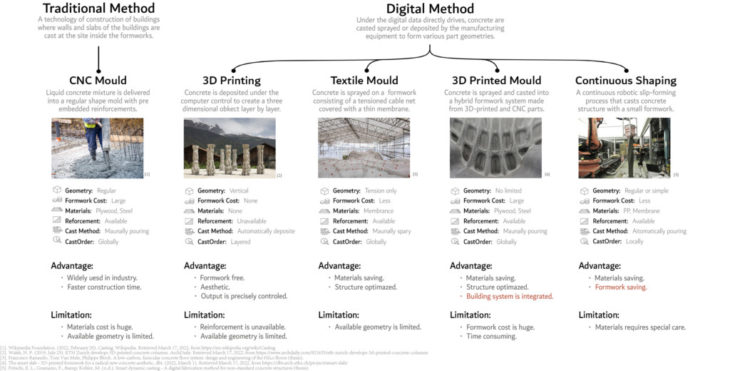
Concrete Fabrication Technique
On the one side, the most traditional and widely used technique nowadays for concrete casting is manually pouring the mixture into the CNC mould. This way for concrete fabrication is cheap and easy. However, this method only available for simple geometries. Furthermore, most of the materials inside the structure are performance less, which means those materials are wasted.
On the other side, there are some other new fabrication technique that could reduce the concrete used, like 3D printing or spreading. However, they also have a lot of limitations in term of economic side or geometry design side.
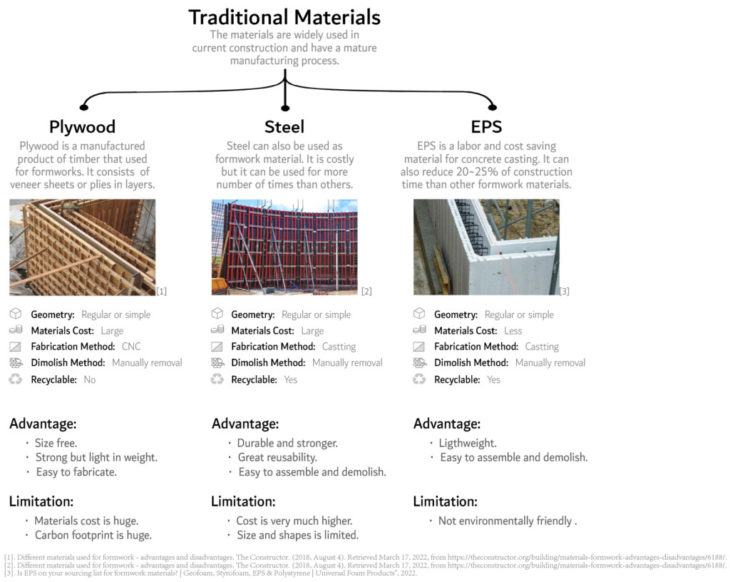
Traditional Formwork Materials for Casting
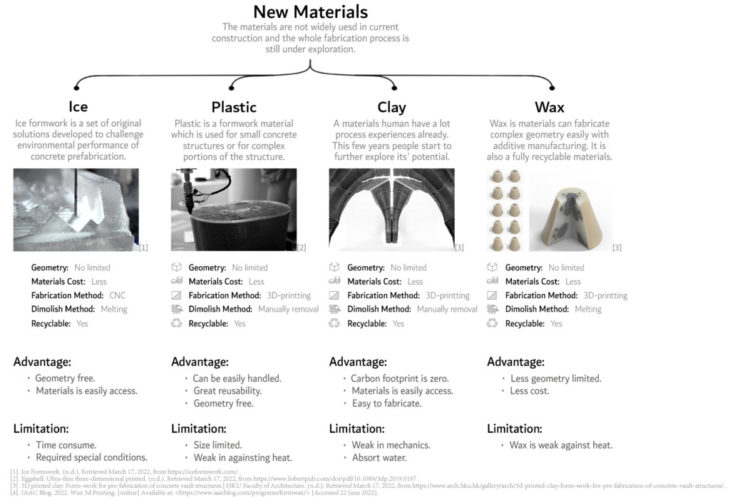
New Formwork Materials for Casting
About the formwork materials, the traditional materials for concrete formwork are plywood, steel and EPS. Although people already developed a mature fabrication system for them in concrete industries. However, those materials are expensive and non- environmentally friendly.
There are also some new materials like ice, plastic, clay and wax. These materials could be fully recycle after used and wouldn’t seriously impact the environment. But compare with the traditional materials, still required further exploration to develop a fabrication system that could implement them into the current concrete fabrication industries.
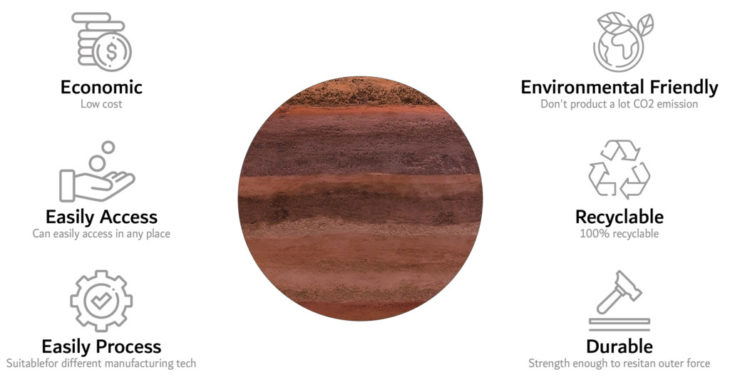
Clay Introduction
After the compared between different fabrication technique and formworks materials. Pouring and casting is still the best fabrication method for concrete in term of structure performance and cost. And I think that clay will be the best materials to match this fabrication method.
On the one side, clay is easily process and access. The new fabrication method could allow everyone in everywhere can easily casting concrete without special skill. One the other side, as a formwork materials, clay is durable enough to stand the pressure from mixture and environmentally friendly after demolishing the formwork.
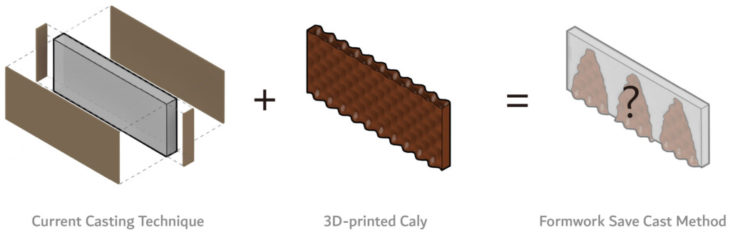
Scientific Interest
So, after the consideration from different perspectives, a question is thrown out: Can we use 3D-printed clay formwork cooperate with traditional casting technique to fabricate complex form castable materials structural elements?
State of the Art
In order to further understand the current stage of applying clay formwork in concrete casting, I researched the projects that were done by other team how they use clay formworks to cast concrete.
State of the Art 1
The first project is 3D printed clay formwork for prefabrication concrete vault, done by HKU. In this project, researchers explore the possibility of concrete prefabrication by the use of clay formwork. The outcome result is the combination of unique aesthetics and structural efficiency. However, they didn’t further explore the available geometry and propose a entire system for the fabrication process.
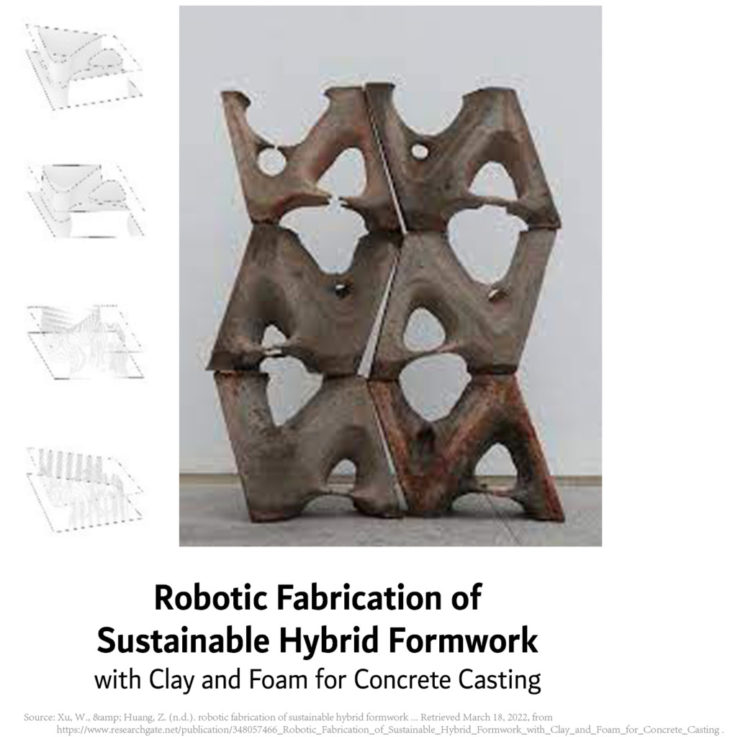
State of the Art 2
The second project is robotic fabrication of sustainable hybrid formwork with clay and foam for concrete casting, done by ZJU. This project propose a hybrid formwork fabrication method utilizing additive manufacturing with clay on top of curved foam surfaces robotically fabricated with hot wire. Although the researchers successfully combine clay with another materials to fabricate the formwork for concrete casting, the accuracy problem is no solved.
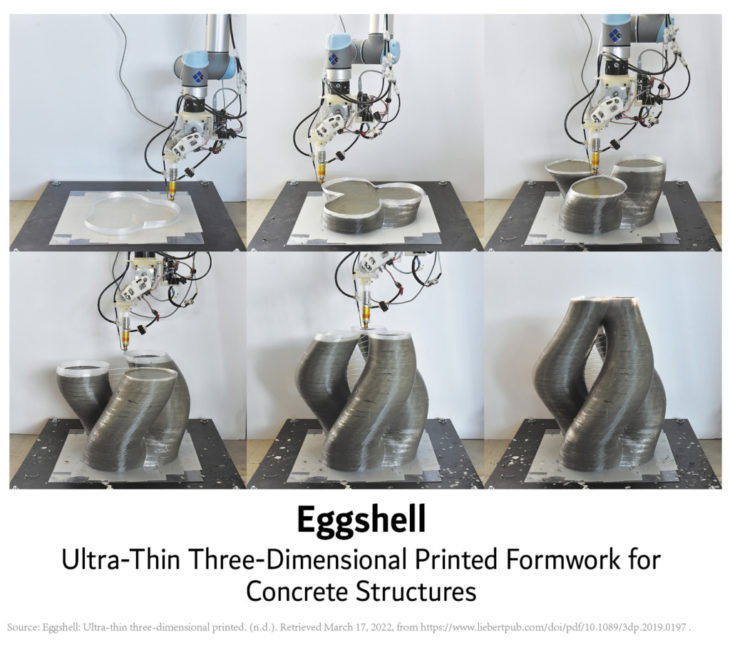
State of the Art 3
The last project is Eggshell: Ultra-Thin Three-Dimensional Printed Formwork for Concrete Structures, done by ETH. Although is no use clay as formwork materials, the Eggshell provides a fabrication process that uses 1.5-mm-thin thermoplastic shell that can be used as a formwork, permitting users to create projects on a large scale, accompanied by robotics in FDM 3D printing.
How to use clay formwork to efficiently cast a complex form structure elements that integrate building systems with less accuracy problem and geometry limited?
Research Framework and Goal
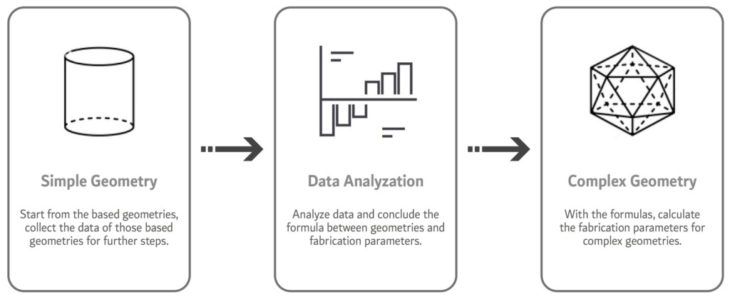
Research Framework
The research framework include three parts: study of casting simple geometries, data analyzation and study of casting complex geometries. Initially, the main goal is to collect the corresponding fabrication parameters for casting the simple geometries with concrete. And then, the main goal is to analyse the data and conclude the formula between geometries and fabrication parameters. Lastly, the main goal is to apply the formula into complex geometries.
Fabrication Test
In order to know what fabrication parameters I need to research, I start from understanding the materials properties of clay.
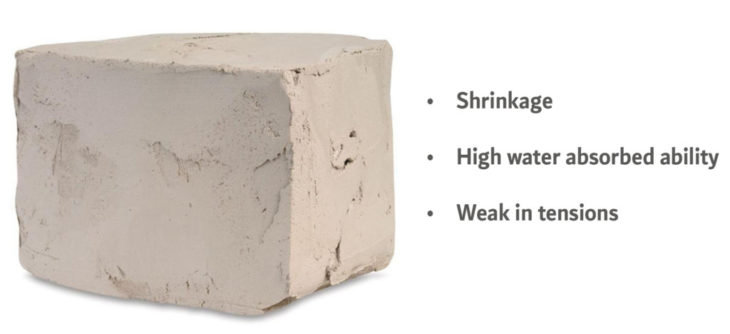
Problem of Clay
Clay is a type of fine-grained natural soil material containing clay minerals. Clays develop plasticity when wet, due to a molecular film of water surrounding the clay particles, but become hard, brittle and non–plastic upon drying or firing. So, I conclude three potential problem of clay: shrinkage, high water absorbed ability and weak in tensions.
From these three potential problems of clay, I developed following three different perspectives I need to further research: shrinkage, stability and assemble.
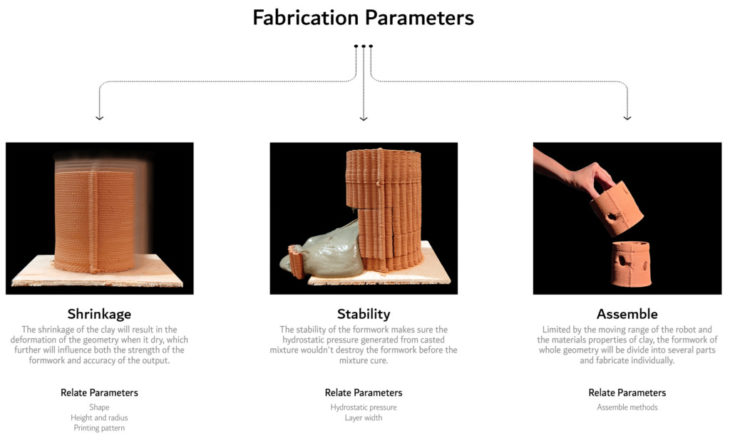
Fabrication Parameters
Shrinkage
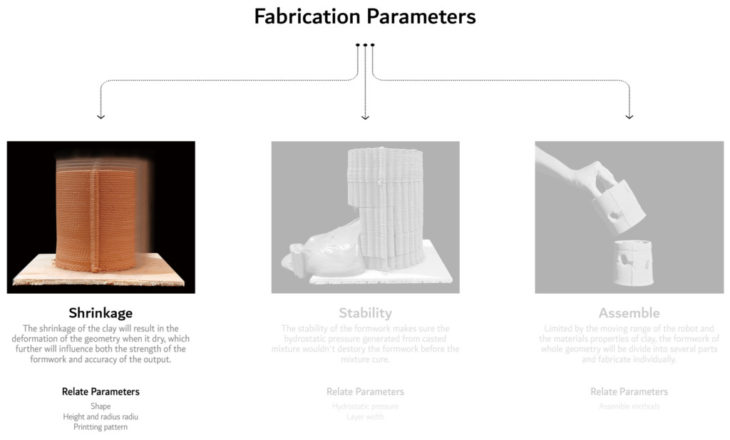
Shrinkage Parameters
In the shrinkage test, there are three relate parameters: the shape of geometry, the height and radius ratio of the geometry and the printing pattern.
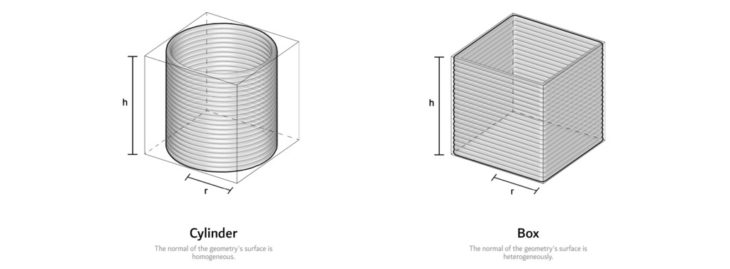
Geometry Set-up
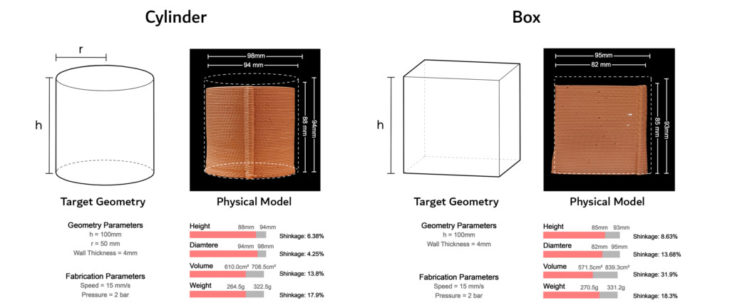
Result
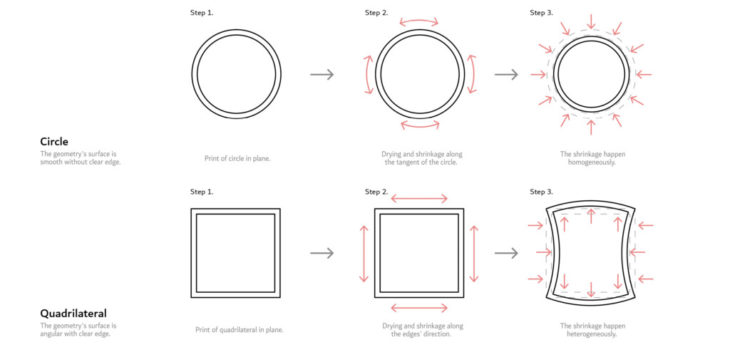
Shrinkage Principle
In the shape testing, I developed two types of geometry: a cylinder with all the normal of the surface is homogenous and a box with four sharp corners. Both samples were measure after printed and after totally dry. A table should those data how shrinkage level is different in two geometries.
After the compare and data analysis, a conclusion was draw: for the geometries with circle in horizontal cross section, the internal force resulted by shrinkage is along the tangent, which means the shrinkage of the geometries will happen homogenously. However, in the geometries with quadrilateral in horizontal cross section’s case, the internal force apply to the geometries is perpendicular from one surface to another surface, which means the corners part will receive the force from two directions, the shrinkage in the corners is heterogeneously. So, the shrinkage is more serious in box=like geometries’ case.
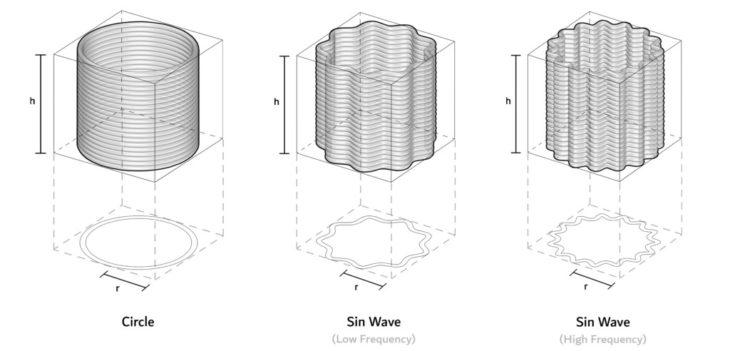
Scale and Printing Path Set-up
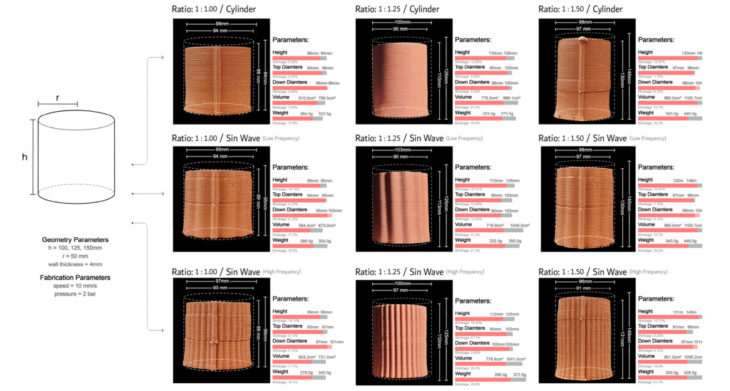
Result
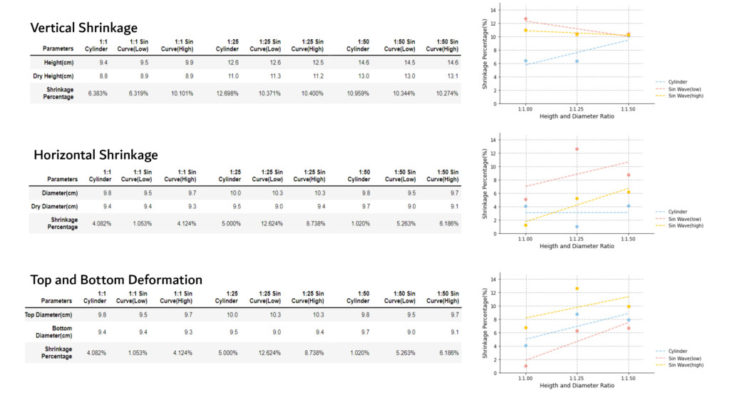
Data Analyse
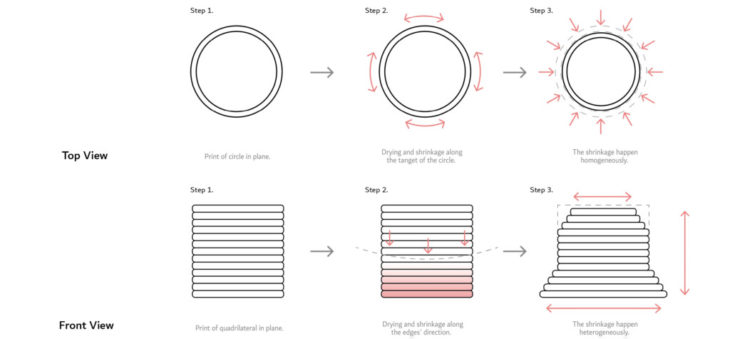
Shrinkage Principle
For the height and radius ratio testing and the printing pattern testing, a series of samples were fabricated with three different height and radius ratio and three different printing patterns. As the first testing, and the samples were measured after printed and after totally dry.
After the regression analyzation, some conclusions were draw? in the vertical and horizontal direction, the shrinkage is linearly uncorrelated to both height and radius ratio and printing pattern. However, the top and bottom deformation is linearly related to the height and radius ratio.
The reason that the top and bottom radius of the geometries is different is that when the printed piece getting dried, the top part of the print is drying faster than the bottom part, the water evaporate from top part of clay will deposit to the bottom part. The clay on the bottom part will absorb the water from top part again. Since the top part clay is dried and solid and the bottom part clay is still soft and wet, the top part will press clay on bottom. After the whole piece is fully dry, the bottom radius of the geometry will be slightly bigger than the top radius.
Conclusion
After the testing for three relating parameters, I draw following conclusions:
1. Cylinders are shrinking less than boxes in the same scale.
2. Different printing pattern affect 5-10% the shrinkage in horizontal in cylinders’ case.
3. The height and radius ratio should be controlled within a special range to control the deformation.
4. A scale factor could be introduced into the design of formwork to avoid the accuracy problem of output causes by shrinkage. In this scale, the vertical scale factor is 1.068.
Stability
For the stability of the formwork, the main relating parameter is hydrostatic pressure. Hydrostatic pressure refers to the pressure that any fluid in a confined space exerts. When the pressure from castable materials is bigger than some values, the clay formwork could be crashed.
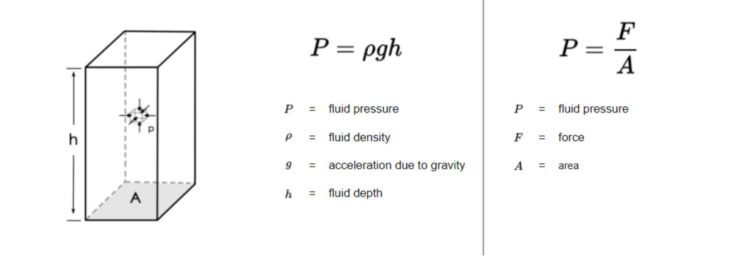
Hydrostatic Pressure Research

Hydrostatic Pressure Research
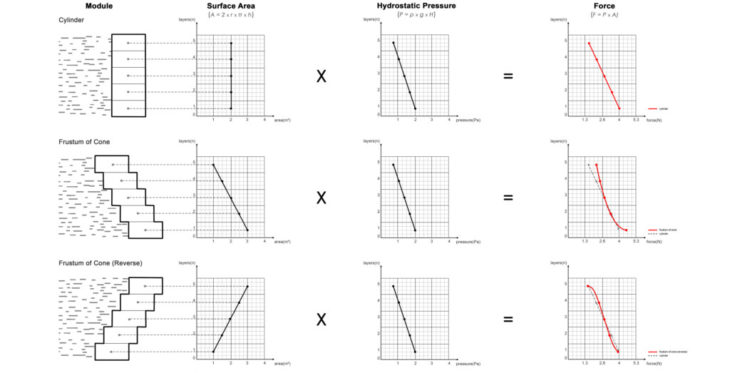
Hydrostatic Pressure Research
In the physical formula, the value of hydrostatic pressure is only related to the density of liquid and the depth of the liquid. Based on that information, I further develop some charts to shows how the force resulted by hydrostatic pressure that apply to the formwork wall will increase with the depth become deeper in three different geometries’ case. In the normal cylinder geometry’s case, the force increases linearly with depth deeper, but in the frustum of cone and the reverse frustum of cone’s case, the force increases quadratically with depth deeper.
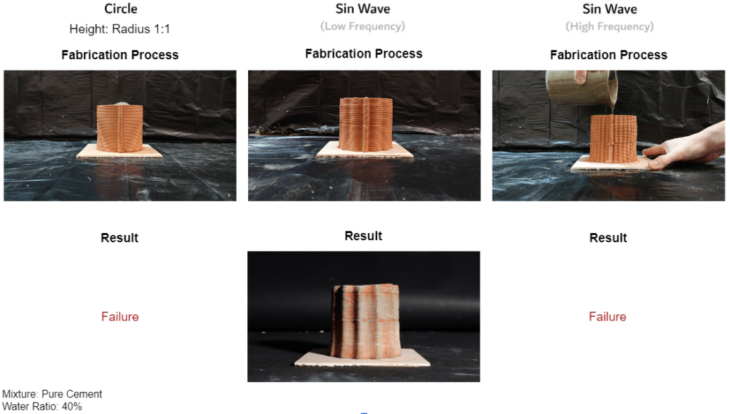
Test Result
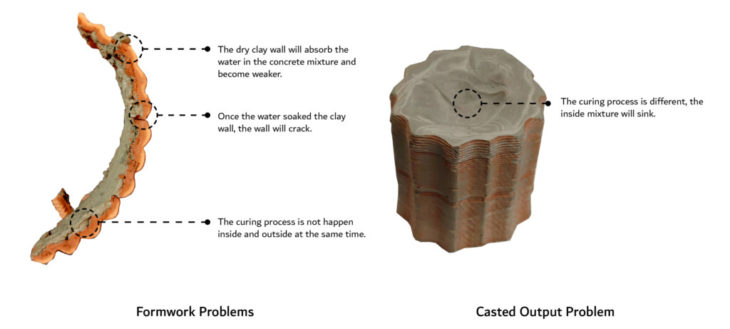
Problem Analysis
The initial stability test is done with the pervious samples for the shrinkage experience. However, only one formwork works in all the samples. From the broken clay wall, I found some problem that may cause the failure: the dry clay will absorb water from the mixture and become weaker. And once the water soaked the clay wall, the wall will crack. Also because the water inside the mixture is no homogenous anymore, the curing process is not happen inside and outside on the same time.
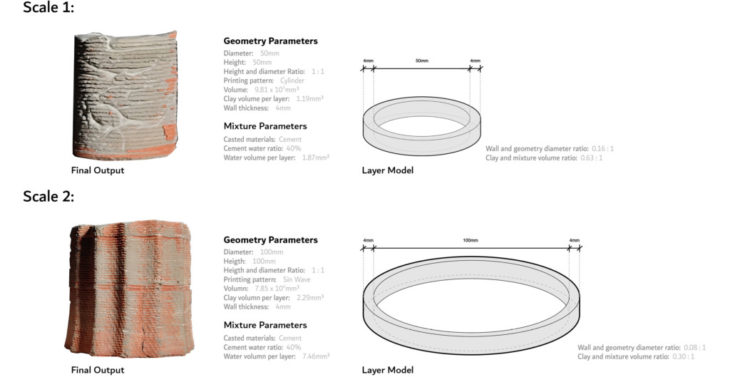
Layer Width Calculation
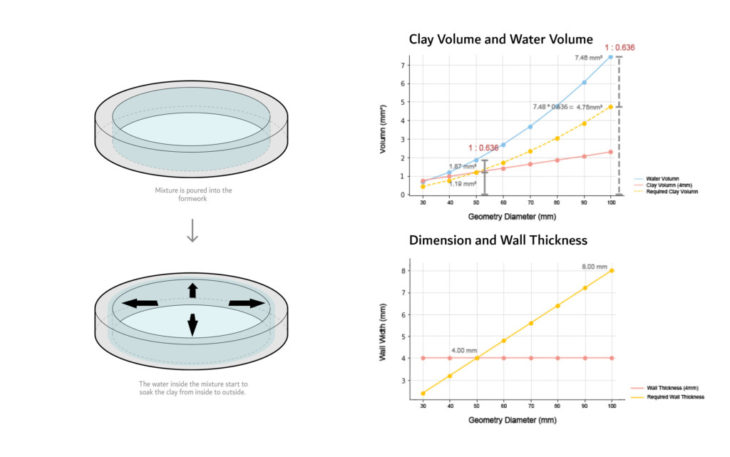
Layer Width Calculation
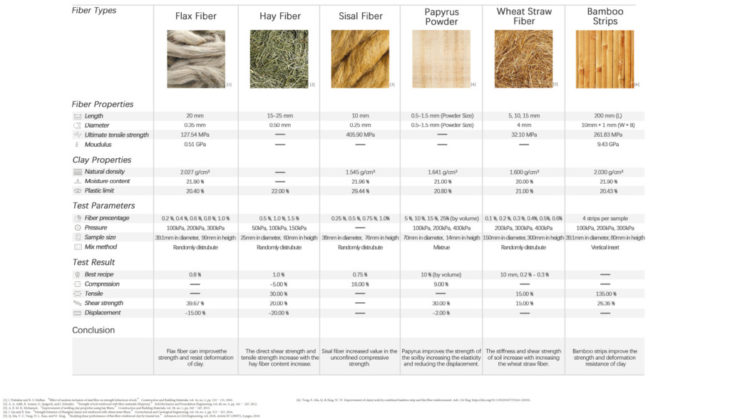
Clay Recipe Modify
Conclusion
After the testing for relating parameters, I draw following conclusions:
- Depending on the geometry, the clay wall thickness should change.
- The clay will absorbs the water from the mixture and becomes weaker.
- Fibre or other materials should be implemented in order to improve the performance of the formwork.
Assemble
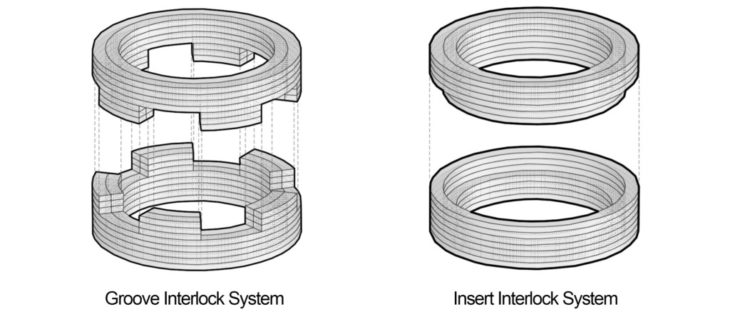
Assemble Methods
Prototype Testing
To proof the conclusions I draw in the previous testing, some prototype were fabricated.
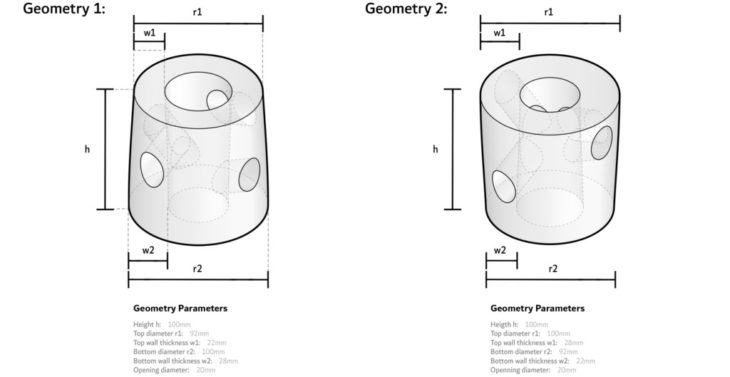
Target Geometry
Conclusion
After the testing for vertical geometries, I draw following conclusions:
- The Clay will absorbs the water from mixture, and the formwork will becomes weaker. Water ratio of mixture should be controlled.
- Bubble exist inside the mixture, vibration bar need to implemented when cast the mixture in order to remove those bubble.
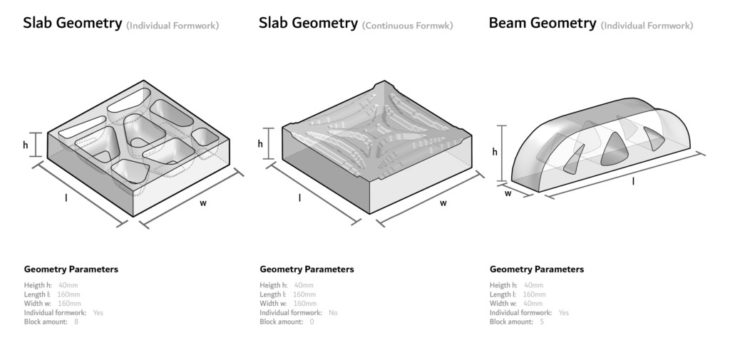
Target Geometry
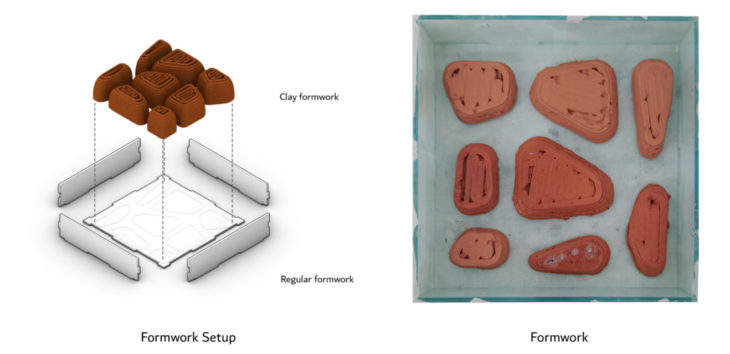
Formwork Set-up
Conclusion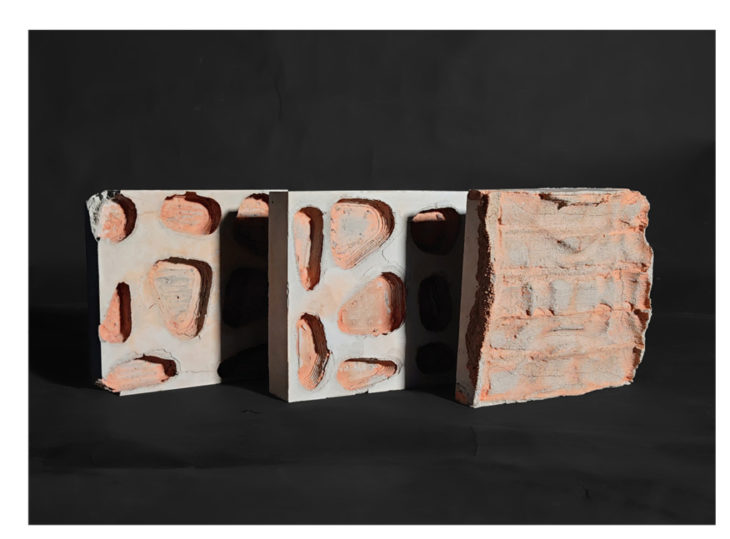
After the testing for horizontal geometries, I draw following conclusions:
- High water ratio mixture will decrease the strength of the materials after it cured. Water ratio should be controlled within 30%.
- Continuous clay formwork could work but requires more fabrication experience and test to make conclusions for ensure the accuracy of casting result.
- Mixture recipes need to improve to reduce the cracking of concrete.
- Reinforcement could be implemented to strength the casted piece.
Prototype Fabrication

Set-up
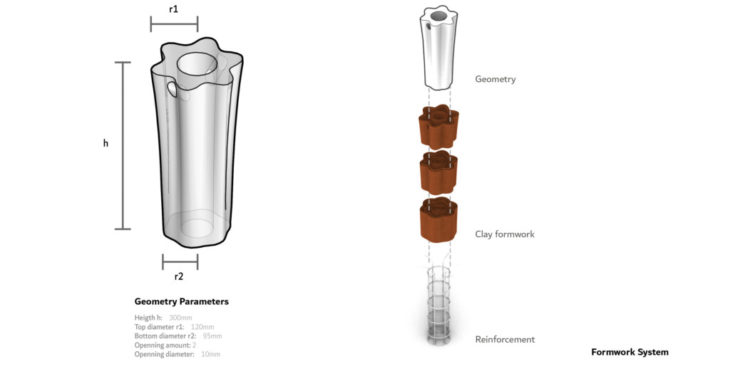
Set-up
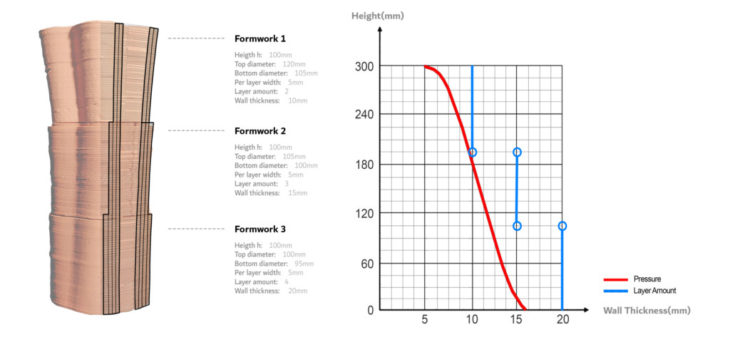
Formwork Cross Section
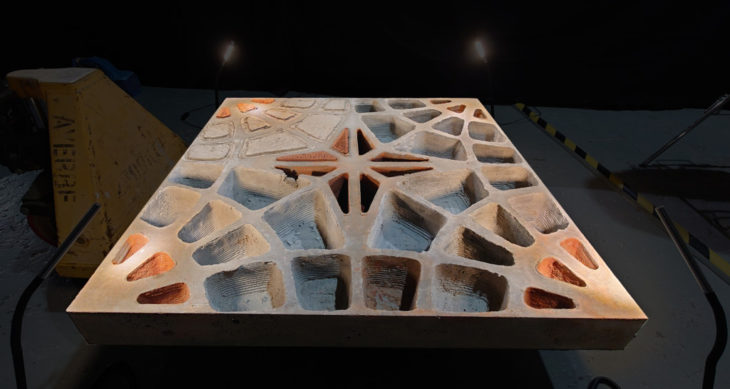
Final Prototype
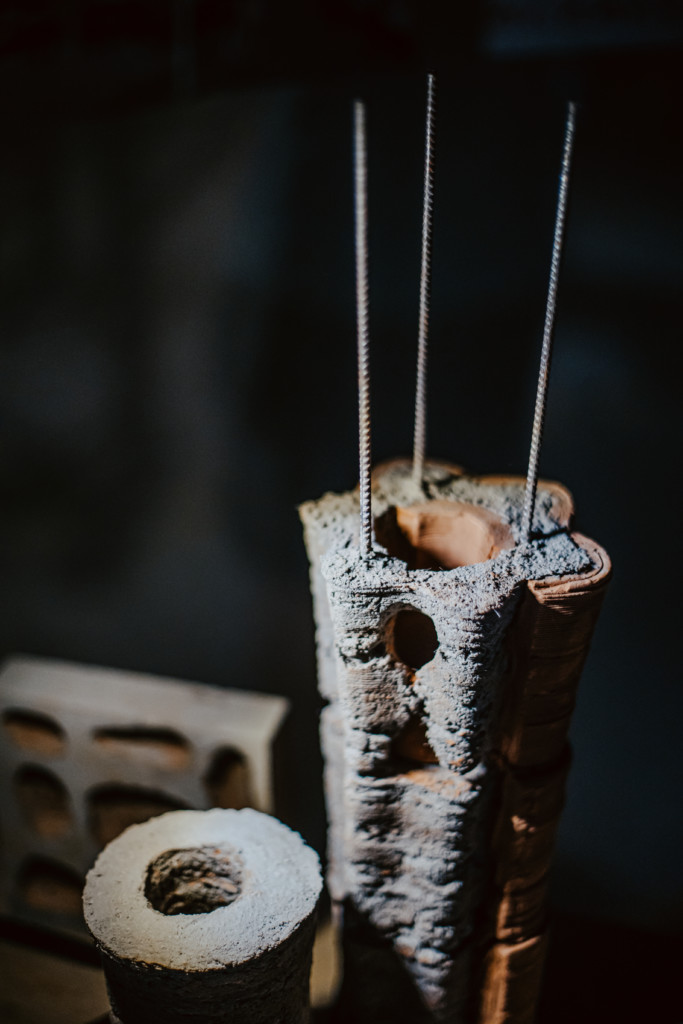
Final Prototype
Cast Green is a project of IAAC, Institute for Advanced Architecture of Catalonia developed in the Advanced Manufacturing Thesis studio, 2021/2022 by Student Liang Mayuqi and Faculty Vincent Huyghe and Gabriele Jureviciutea