The project is a second phase of the course on digital fabrication. Initial task is with set spatial dimensions and fabrication materials and technique to design an architectural object – a spaceframe – that would work as a divider in IAAC workspace. It has to perform well with both sides, create a transition and mediation between emerging sub-spaces. The task is performed in a groups of four students in the span of a month and is executed in 1:1 scale.
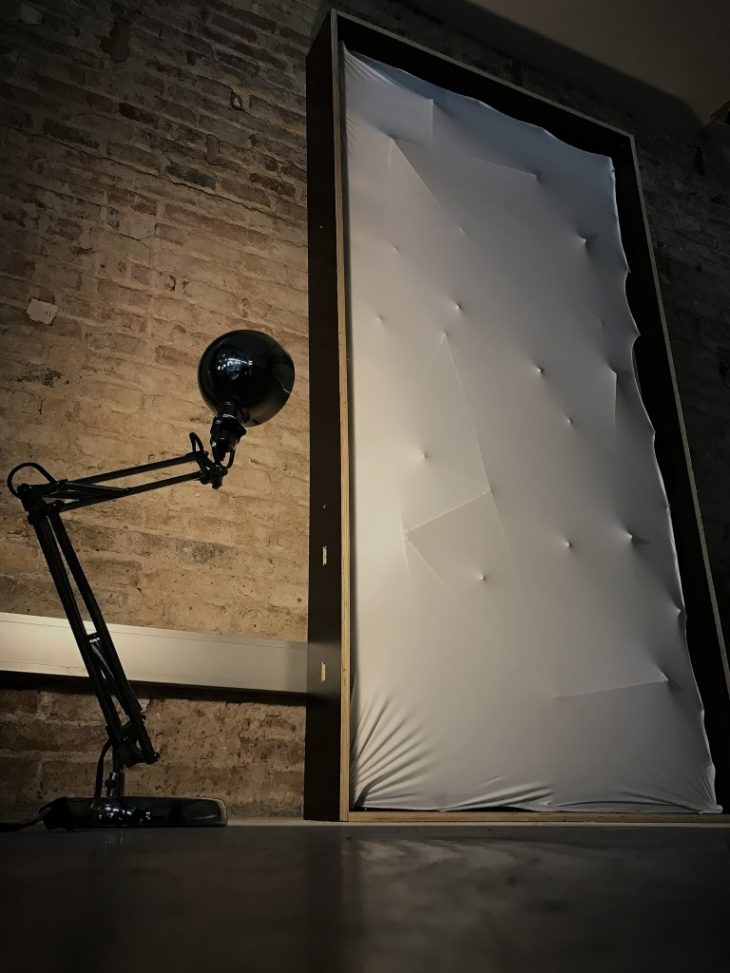
Result – Foggy Spaceframe / Digital Fabrication IAAC
Foggy Separator is an exercise on creating a spaceframe with 3D-printed structural nodes and fibreglass rods that are covered with a white elastic fabric. The main objective is to work with light visual effects both in the space itself and potentially with the lights incorporated in the structure. The main potential of exploration lies with the detailing of the nodes, integrity and performance of the structure and the visual effects.
Inspiration
One one hand, inherent potential of the fabric to stretch is commonly used in the tensile class of structures – a structure only caring tension forces and no compression or bending. The attachment points can either push or pull the surface which in term under load take the most efficient shape for the given physical performance creating very stable spatial structure.
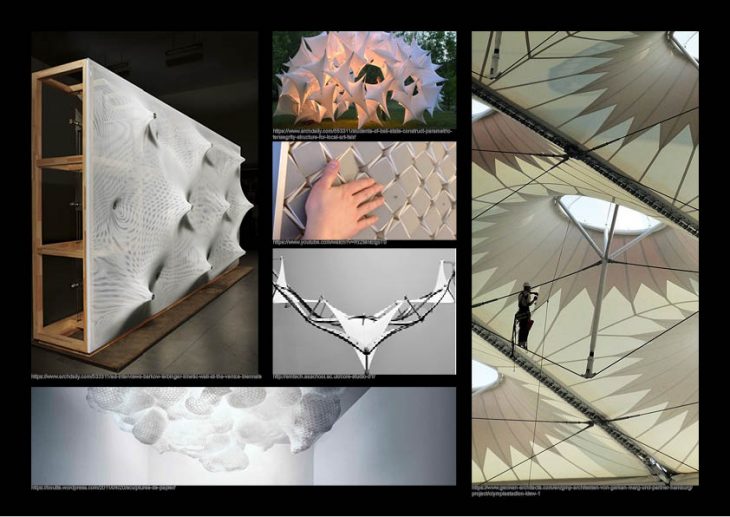
General references – Foggy Spaceframe / Digital Fabrication IAAC
On the other hand, the inner system has has to operate on a more fixed type of behavior. It has to consist of independent joints and the connecting rods in between. The scale of the spaceframe and the time constraints call for minimizing the size of individual elements. However, at the same time this incrases the amount of the nodes required to fill in given space. While the rods can be rather flexible given small enough radius , instead, we decided to use it’s strength as the force-caring element. In this case, the nodes mainly are intended to hold the rods together.
Joint references – Foggy Spaceframe / Digital Fabrication IAAC
Thus, the combination of flexibility of the fabric and rigidity of the inner structure became the core principals we decided to focus our design on. Despite the inner structure not being on the display interaction with the frame and light effects from outside and/or inside between the pieces of the cloth provide the depth of experience as well as potential for unconventional visual effects.
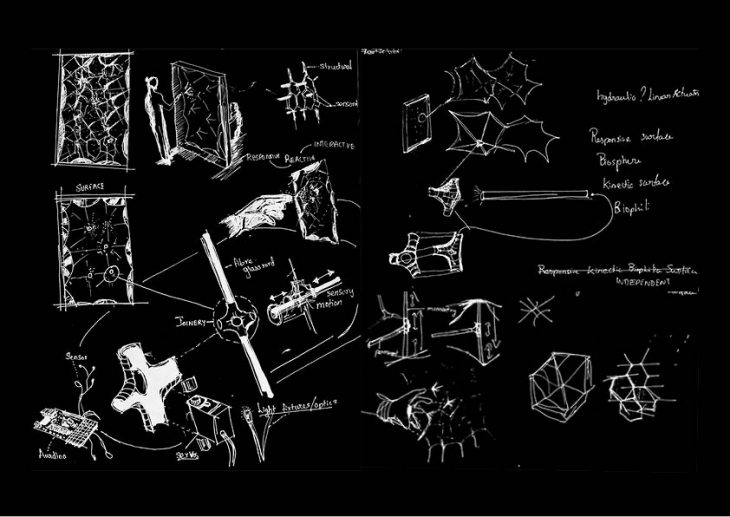
Sketch – Foggy Spaceframe / Digital Fabrication IAAC
Development
Fist of all, the initial solution tested mainly the tensile component of the structure. The nodes themselves had no variability though could adapt and change with different design of the frame in general with the length of the rods. The rods would work in three functions: holders between the nodes, fabric pushing elements and interactive movable elements. However, the size of the element would not allow for scaling of production and did not address requested by task variability of patterns. The tandem of the node and rods performed well in the fabric serving as a proof of concept. This allowed further investigation into the system itself.
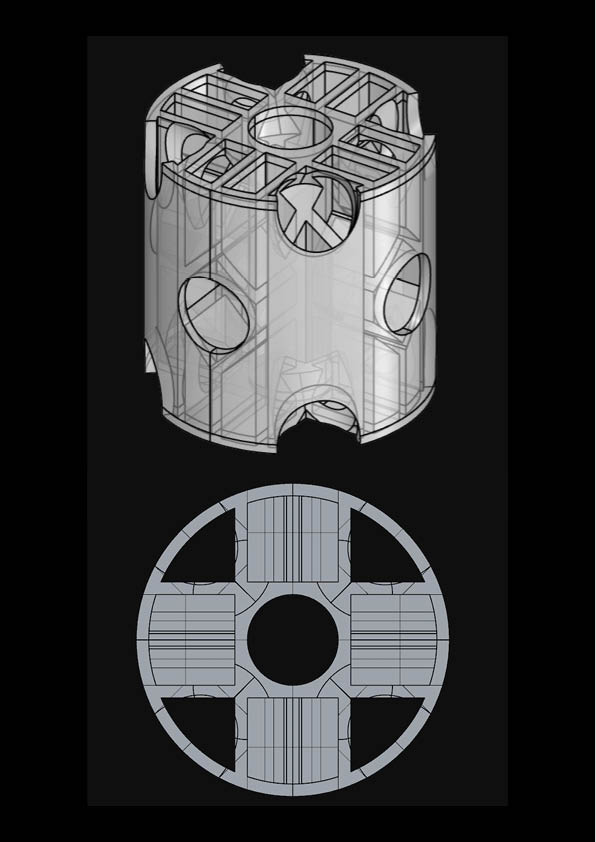
Prototype 1 – model – Foggy Spaceframe / Digital Fabrication IAAC
Prototype 1 – Foggy Spaceframe / Digital Fabrication IAAC
Secondly, we resolved the problems of the prototype with two interlinked main changes. Substantial scaling of individual joints allowed to variate each of the nodes outgoing connections. Additional types of nodes were created to protect the fabric from tearing by the rods. As a result we introduced a complete system we could now use to design a solution for the frame.
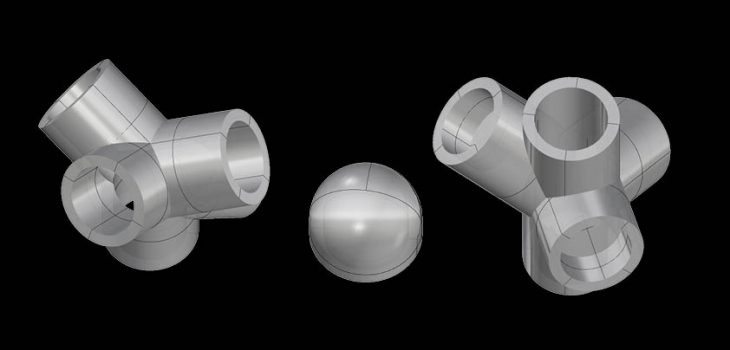
Prototype 2 – model – Foggy Spaceframe / Digital Fabrication IAAC
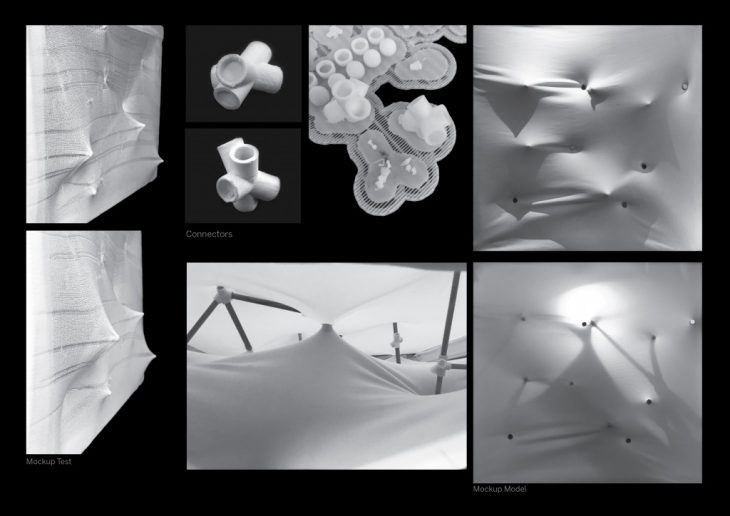
Prototype 2 – Foggy Spaceframe / Digital Fabrication IAAC
The idea behind the overall scheme was to create areas of changing density with randomized position of the joints and directions of the rods. The surface, given mostly opaque quality of the fabric, played important role. We used points, edges and two-dimensional shapes in contrast as starting point of the spaceframe design. Overall structure is well inside the dimensions of the frame. Furthermore, with light effects of shadows and our intention to encourage interaction with the architectural object, the depth of the structure is fully developed as well and even plays dominant role int the final design.
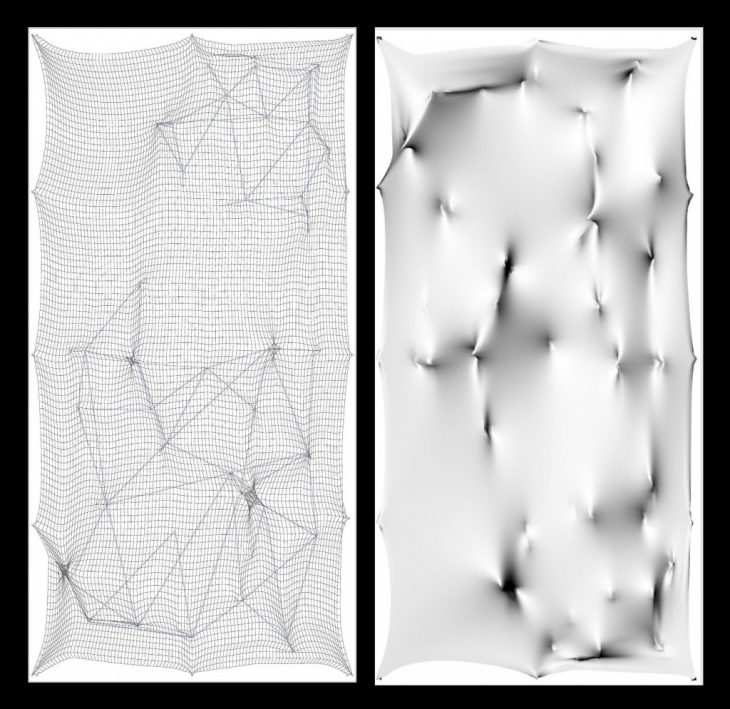
Diagram – Foggy Spaceframe / Digital Fabrication IAAC
The solution was supported by the parametric design tool of Grasshopper. The model is designed by generating clouds of points, selectively connecting them and for each point generating individual joints. After testing the 3d printing of the elements, the script was adapted to orient the nodes in the way to minimize the amount of supports necessary for the print – by aligning two of the outgoing connections with the surface instead of placing it standing on one of the “legs”.
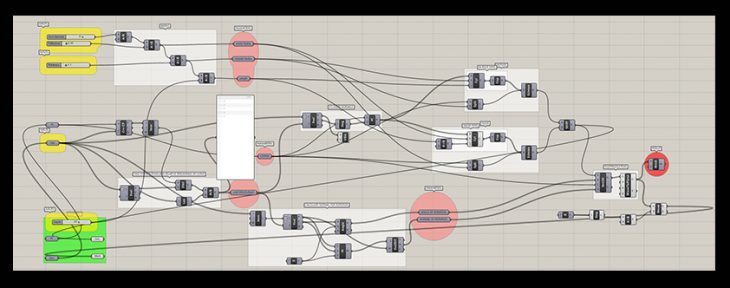
Script – Foggy Spaceframe / Digital Fabrication IAAC
For the assembly part an Alphanumeric system was developed. Each joint got unique name in form <letter><batch of print>. Each rods subsequently got the name from the nodes it was connecting.
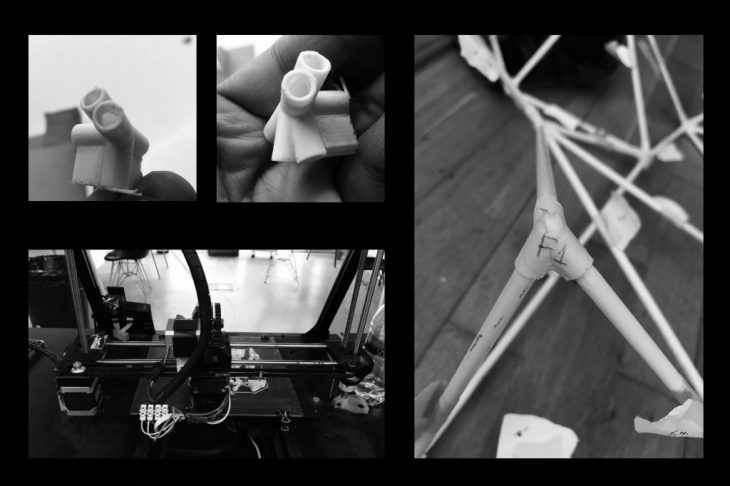
Process – Foggy Spaceframe / Digital Fabrication IAAC
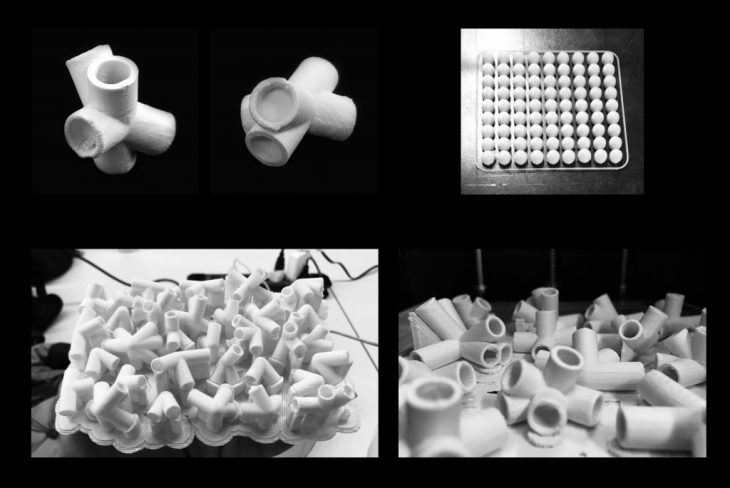
Process 2 – Foggy Spaceframe / Digital Fabrication IAAC
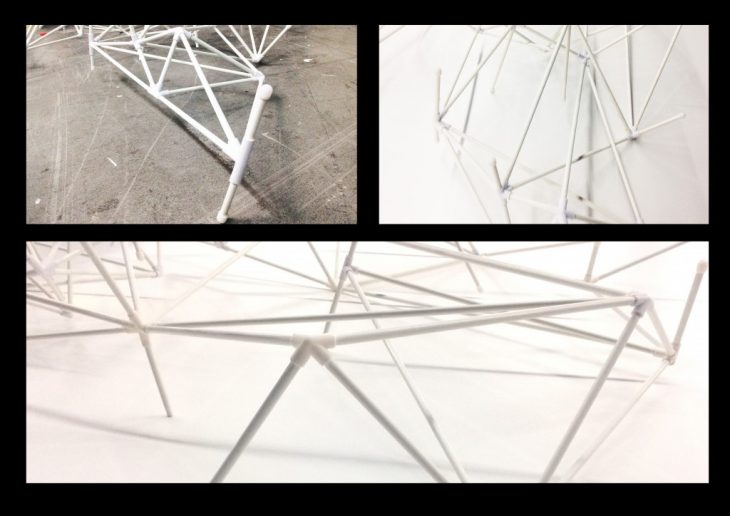
Assembly – Foggy Spaceframe / Digital Fabrication IAAC
Spaceframe
Printer: Zortrax M200
Materials: Z-ABS (white), Z-PLA Pro (white), Z-HIPS (white), Z-ABS (white)
Print Time: 3h 46min + 15h 10min + 6h 59min + 2h 25min
Print Material Weight: 32g + 107g + 44g + 15g
Print Material Length: 13.12m + 33.42m + 17.59m + 6.43m
Support content: 0% + 38.51% + 0% + 12.91%
Total time: 28h 20min
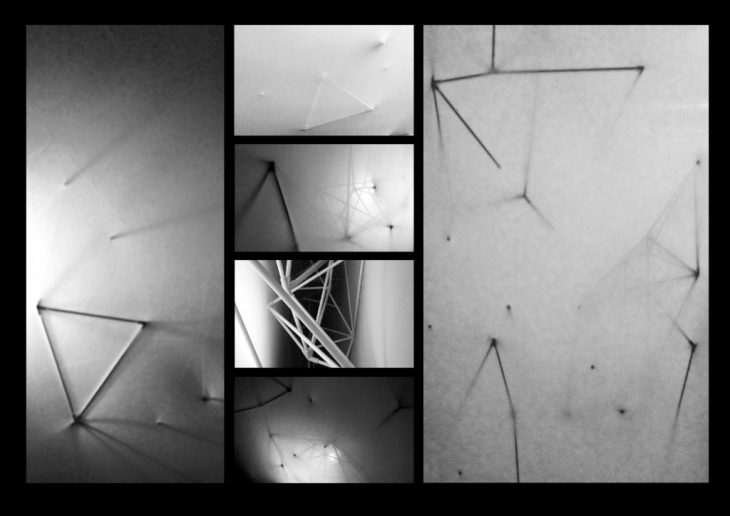
Result details – Foggy Spaceframe / Digital Fabrication IAAC
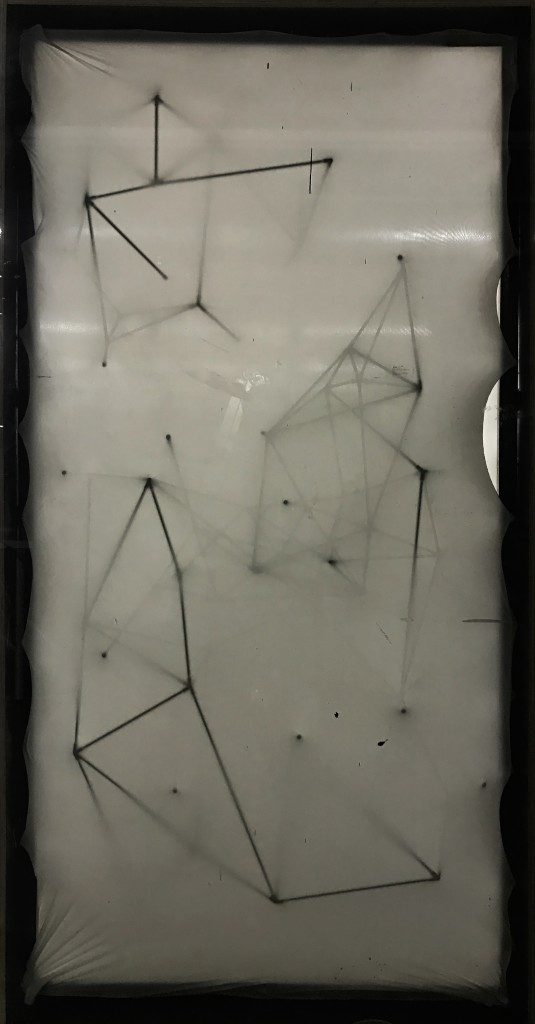
Result Close-Up – Foggy Spaceframe / Digital Fabrication IAAC
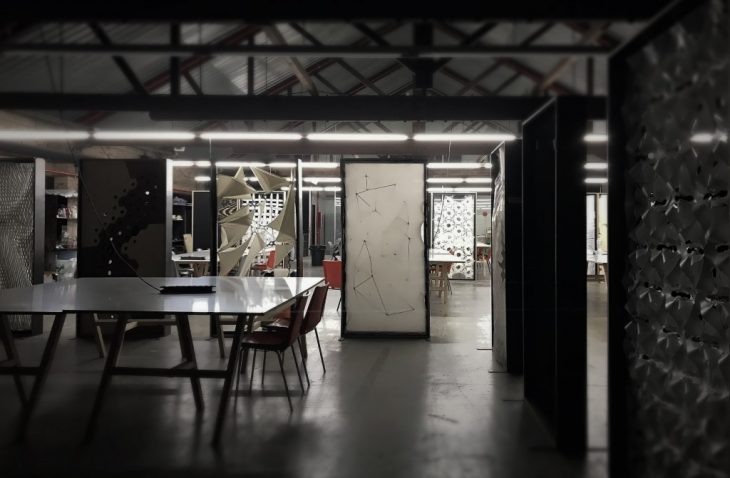
Result in Context – Foggy Spaceframe / Digital Fabrication IAAC
Conclusions
To sum everything up, the use of 3D-printing technology coupled with parametric digital design allows us introduce massive variety and unseen complexity with no additional cost in fabrication. This potential however comes at the price of potential complication of assembly process and requires shift in approach and special attention in the design phase.
The design is not limited to the given solution but rather introduces a flexible system of space structure. Moreover, explored system maximizes both use of the technique and of the materials. As such, the fabric does not just play a role of a visual separator but a structural element actually holding the frame in mid-air. The geometry of the system itself provides rigidity once fully assembled allowing to minimize the use of material in the nodes saving both in cost and in time of production.
The potential of future experimentation lies with further development and implementation of not only pushing but pulling force centered elements, fabric use, as well as accounting in the design for extra-force the nodes take during the assembly stage by gradual thickening the core part of the nodes.
Digital Fabrication // Wall Panel is a project of IaaC, Institute for Advanced Architecture of Catalonia
Developed at Master in Advanced Architecture in 2017 by:
Student: Daniil Koshelyuk, Jasser Joan Salas Castro, Nustrat Tabassum, Ifthikar Mohamed Noordeen
Faculty: Alex Dubor, Raimund Krenmuller, Ricardo Valbuena, Ricardo Mayor, Kunaljit Singh Chadha.
* Pictures with references contain source links.