A Call for Alternatives
The innovations in the last two centuries have led us to an era in construction where materials are stronger, more versatile, and easier to produce than ever before. These advancements, however, have come at a cost. As new technologies have been developed over the centuries, for most of them, little thought was given to their entire life cycle, the role their embodied energy would have on our environment, and the waste they would create.
Whilst this applies to many of the super materials that have become status quo in architecture, petrochemicals are particularly insidious. Since the advent of their production at industrialized scale in the 1950s and ever increasing use in the decades since, plastics’ exceptional properties have granted them access to every facet of our built environment – not only in the material involved in the ultimate construction of our built environment, but in all steps of a material’s lifecycle – and their use as such has led to their waste becoming a global catastrophe.
Their ever-increasing presence in all aspects of life, as well as their useful lifespan to overall life ratio, has allowed plastic waste to accumulate in every niche of our environment. Plastics have even now made it to the most remote and discrete parts of the planet – from the shopping bags found floating around the bottom of the Mariana trench to micro- and nanoplastics being found in water tables and throughout the food chain.
Fortunately, society as whole has begun to come to grips with this monster we’ve created, and many of the emerging technologies, materials, and methods we see today attempt to address the unsustainable practices of modern day construction. This exploration sets the approaches of 3 projects/products in the light of addressing material waste, their unique direction, and the potential these new materials, processes, and paradigms have within the construction industry.
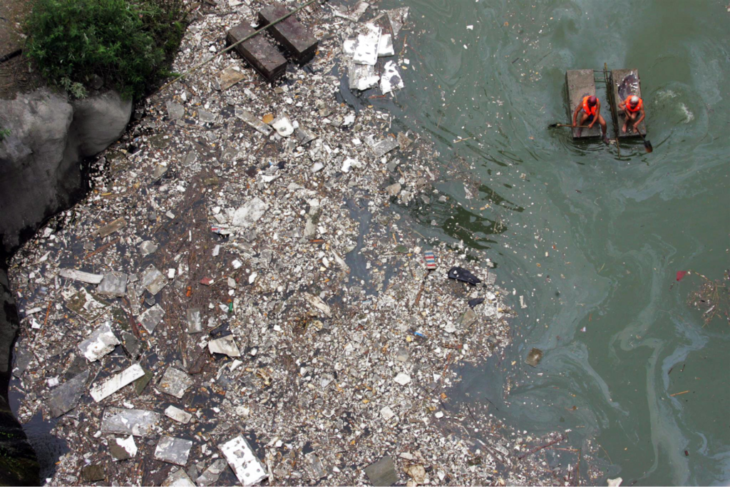
Source: UNEP
“The construction sector is the second-largest consumer of plastic resins globally .. and its consumption has been growing at a rate of 4.3% per year for the past two decades.. Even in the most advanced circular economies, where industries are actively pursuing plastic recycling, fewer than one-sixth of new products are made from recycled materials....in many cases, reclaimed plastic is of lower grade than virgin plastic, and ‘recycling’ actually means that plastics are downcycled....recycling is further constrained by additives in plastics from previous decades, which are now known to be toxic. “ (Pickard and Sharp, 2020)
State of the Art
The study looks at the material innovations of three projects/products and their approach to this problem, respectively:
- NPSP: Implementing biocomposites into the current architectural vernacular
- Pulp Faction: Developing new methods and materials from the bottom up to inform a new architectural paradigm
- Cellulosic Biocomposites: Change in Manufacturing cycles to inculcate these new materials for large scale applications
The Focus has been placed on three varying degrees of reshaping how we build. These different perspectives each have their own advantages in terms of adaptability, scalability, and viability as long vs. short term solutions.
Bioplastics
NPSP develops and supplies innovative environmentally friendly composite materials and products for public space, construction, design and mobility. They use bio-based and circular raw materials as much as possible, which can be reused after a long lifespan.
NPSP realizes solutions in bio-based composites and uses high-tech production technology for everyday applications in natural fiber reinforced plastics. They want to play a leading role in making our society more sustainable by demonstrably reducing the environmental impact and by providing expert advice.
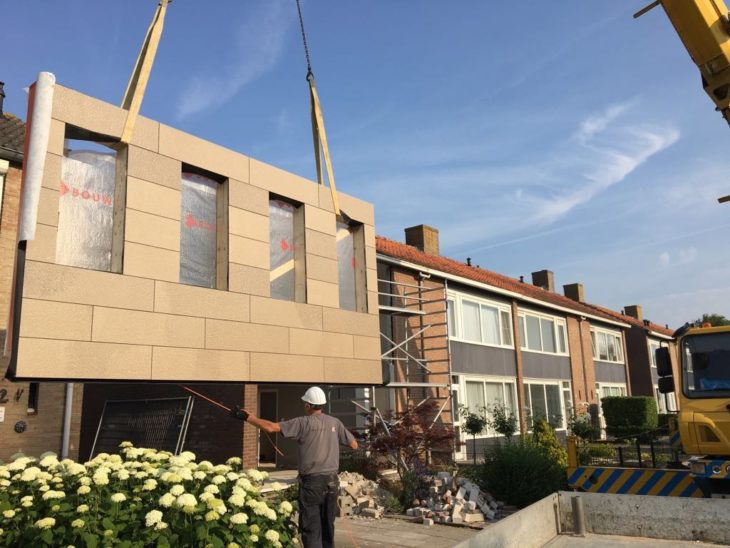
Prefrabicated biocomposite cladding. Source: NPSP
The footprint of their product is 5x less than aluminium in ways of production and recycling.
- No fossil fuels are used
- Lower carbon footprint
- Mostly biodegradable or recyclable
In an interview with Mark Lepelaar, owner of NPSP, the products and approach of NPSP are explained in further detail:
Q: After the material is being used, what options do you have?
Interview with Mark Lepelaar from NPSP
Q: Is the material 100% recyclable?
Interview with Mark Lepelaar from NPSP
There are many parameters which could help or hold up the scaling of the use of these materials.
- The costs are high and the market share is low. When the costs would go down, the market share could rise and either way around. Fabrication would be on a higher level and the prices could decrease.
- The material properties are not the same as other common materials in construction. Because of this, the design has to be adapted when bioplastics are used.
- Government policies could help make these materials more interesting. For instance: using tax on carbon would make steel materials less attractive.
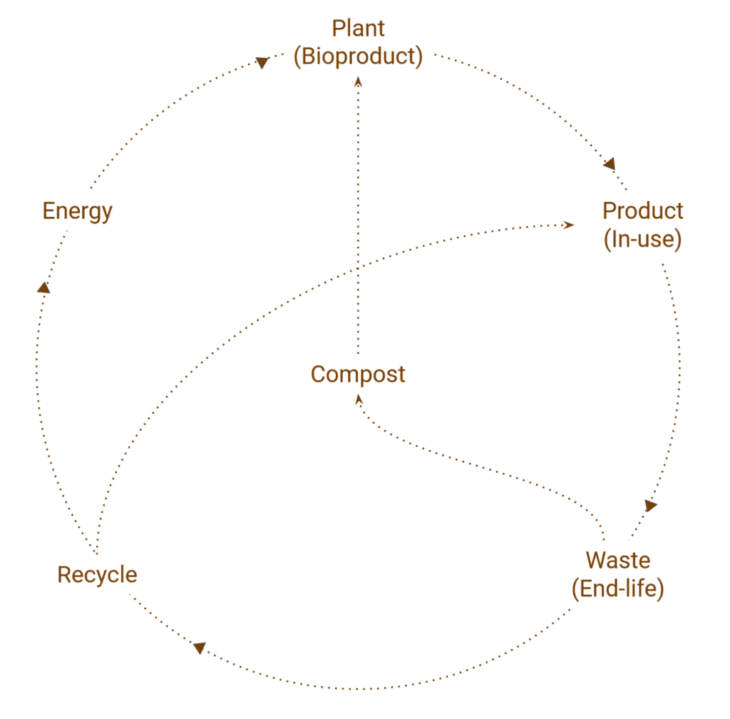
Closing the loop of bioplastics
Pulp Faction
In an exploration conducted by the bioDigital Matter Lab at Lund University, the team of Ana Goidea, Dimitrios Floudas, and David Andréen leveraged mycology to aid in 3D printing a column.

Source: Lund University
The extruded material consists of a wood and paper pulp and kaolin clay mixture along with a thickening agent as the main structural scaffolding. This pulp was first heated in an autoclave to remove any impurities and subsequently inoculated with mold spores – namely white and brown rot fungi in separate instances. The fungus infused material was allowed to sit for a week to let the fungus propagate before the extrusion process and was left to incubate again for 10 days after extrusion whilst the mycelium continued to grow. After this growth stage, the biocomposite was desiccated to stop the growth process.
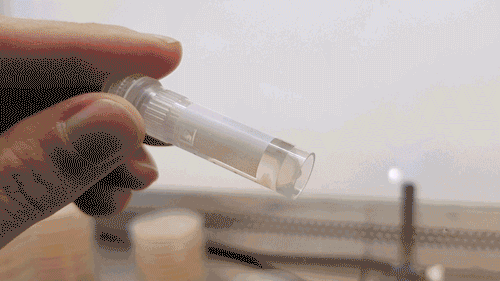
Source: Lund University
The mycelium as a binding agent, alleviating the need for synthetic, i.e. petroleum-based plastics. Through their investigation, the team determined that the mycelium does in fact lend value both structurally and in hydrophobicity in comparison to a non-inoculated control specimen.
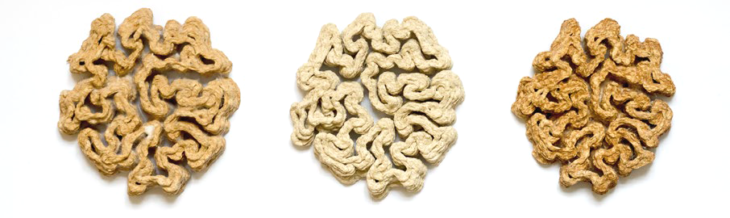
Source: Lund University
The application of additive manufacturing in this exploration allows a greater design flexibility than the use of other manufacturing techniques. The overall design of the column utilized a Gray-Scott reaction diffusion pattern to allow for thinner walls and facilitate air movement throughout the piece, which is important in promoting mycelium growth.
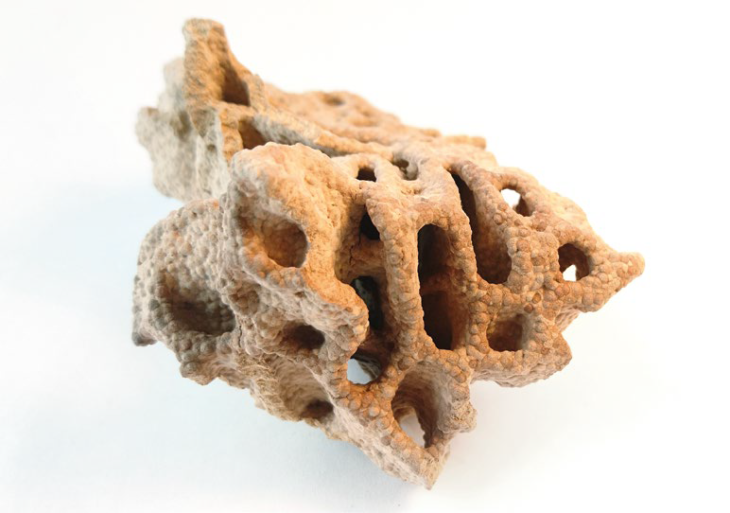
Source: Lund University
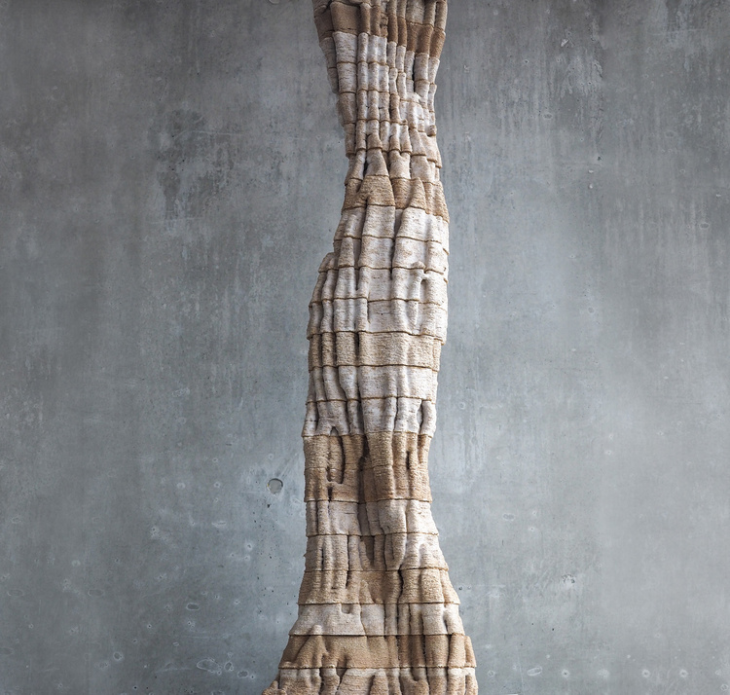
Source: Lund University
Although not a directly scalable or architecturally applicable solution, this study offers a valuable alternative in its approach to architecture and construction. By examining and experimenting with non-traditional materials such as mycelium, designers can begin to build on these alternative advancements – which has the potential in compounding towards a major shift in our collective architectural thinking and methodologies and improving architecture’s impact on the environment. The most crucial suggestion that we should consider is that it is not just possible, but perhaps imperative that we redefine our approach to building.
Cellulosic Biocomposites
“Large scale additive manufacturing with bioinspired cellulosic materials” was a research experiment conducted by a team of varied disciplines and fields of construction and technology namely Naresh D. Sanandiya,Yadunund Vijay , Marina Dimopoulou, Stylianos Dritsas & Javier G. Fernandez. This work was supported by the International Design Center (IDC) at the Singapore University of Technology and Design, the SUTD Digital Manufacturing and Design Centre (DManD), and the National Additive Manufacturing Innovation Cluster (NAMIC), Markus Hesse from JELU-WERK GmbH & Co. KG for the donation of the cellulosic materials used in this study.
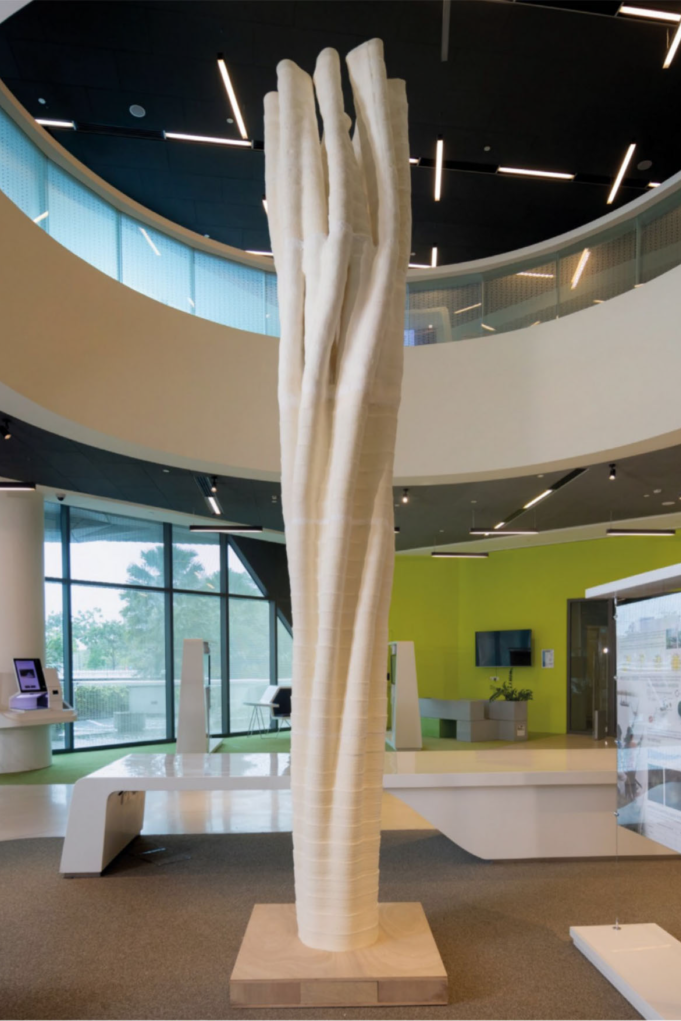
Source: Singapore University of Technology & Design
The objective of this research is to apply the principles of the cell wall of fungi and oomycetes to produce a general manufacture system based on three premises:
(i) The resulting bioinspired composite must be made by its natural constituents;
(ii) Components must be available and abundant in every habitat on earth;
(iii) Cost, environmental impact, and scalability must enable generalized use.
Due to recent research on the oomycetal walls we know that chitin and cellulose produce structural composites in their natural form, without being regenerated, and therefore the criteria (i) and (ii) are theoretically possible. Additionally, both molecules are common indus-
trial byproducts with a combined cost in the range of commodity plastic, being exceptional, and probably unique, biological candidates to fulfill criterion (iii).
One such iteration was named FLAM.
The next steps in the study were to understand the pliability of FLAM and how well it can retain shape and deploy it for a 3D printing fabrication workflow.
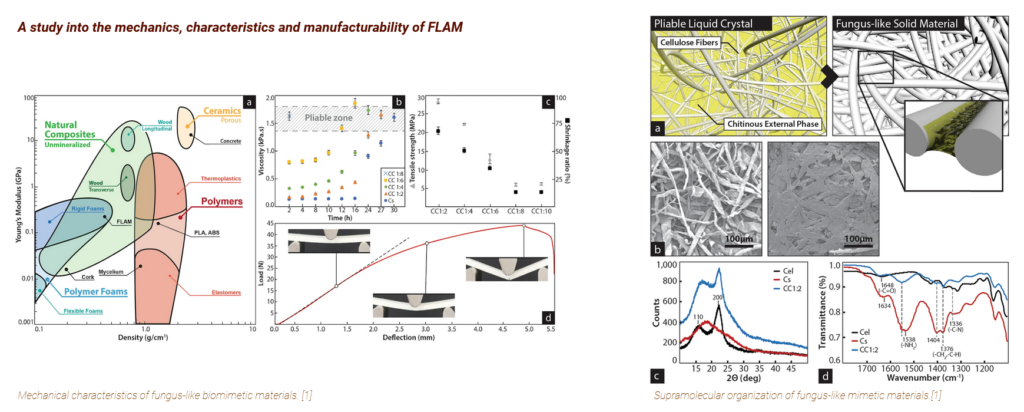
Source: Singapore University of Technology & Design
After solidification, composites with low amounts of chitosan (<8%) show slender mechanical properties, attributable to its inability to fully bind the cellulose fibers. In contrast, high amounts of chitosan (>17%) produce strong internal forces as the polymers loses water and shrinks, under-mining the integrity of structure.
An inherent optimal ratio of 1:8(w/w) chitosan:cellulose, produces a pliable composite, where no removal of water is required, with minimum shrinking and an unexpected low water uptake.
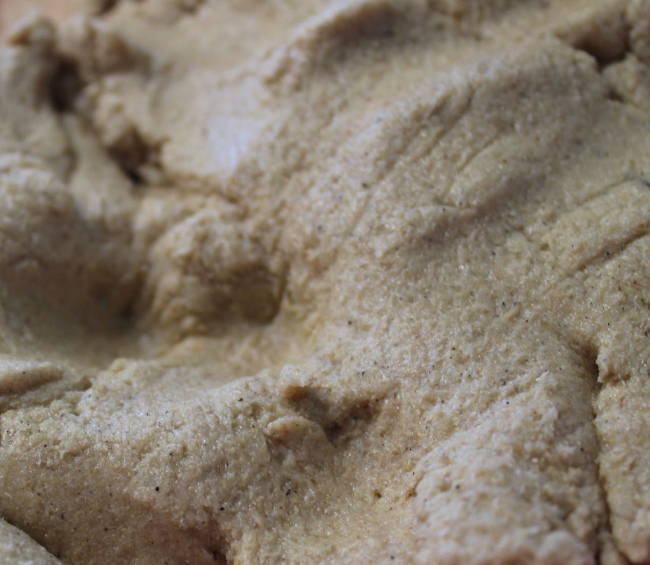
Source: Singapore University of Technology & Design
Due to its abundance and biodegradability, the use of cellulose in a versatile manufacturing approach such as additive manufacturing has broad technological and economic implications. In spite of extensive past and current research to adapt cellulose to 3D printing, progress is still riddled with obstacles such as use of hazardous solvents, lyophilizing small cellulosic scaffolds and contamination by mixing the polymer with commodity plastics.
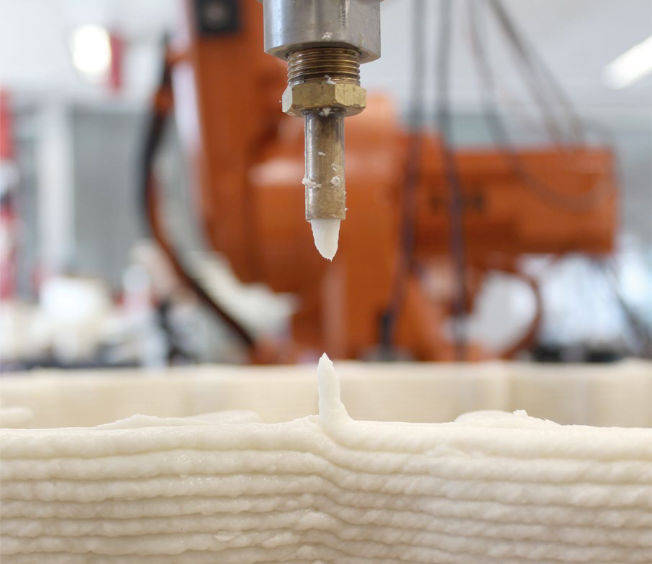
Source: Singapore University of Technology & Design
To demonstrate the free-form fabrication capability, material strength, assess the reliability of the extrusion system and understand the workflow, they developed an architectural-scale prototype pillar of 0.6-1.0m diameter and 5m height.
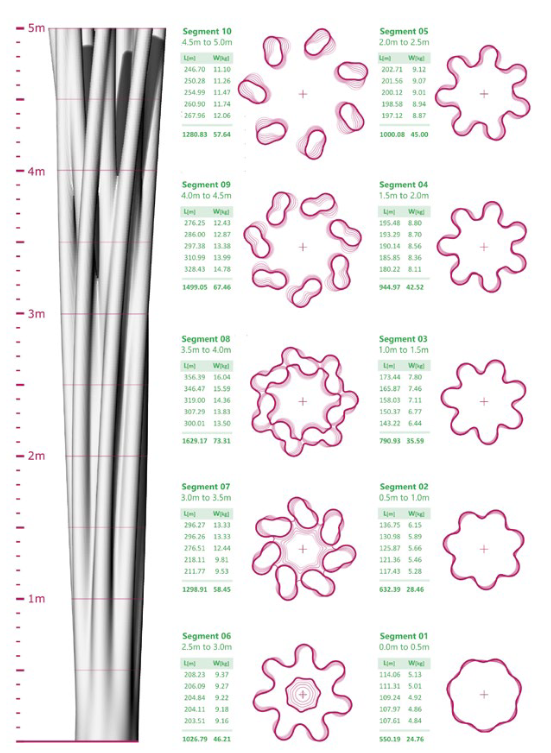
Source: Singapore University of Technology & Design
The form was split into 50 vertical segments of 250mm height, taking 30-120min each to print. Segments are composed of two adjacent filaments with wall thickness of 25mm. Alternative wall structures were tested such as incorporating buttress fins or an internal web pattern for increased stiffness but the double filament wall design was the most time efficient.
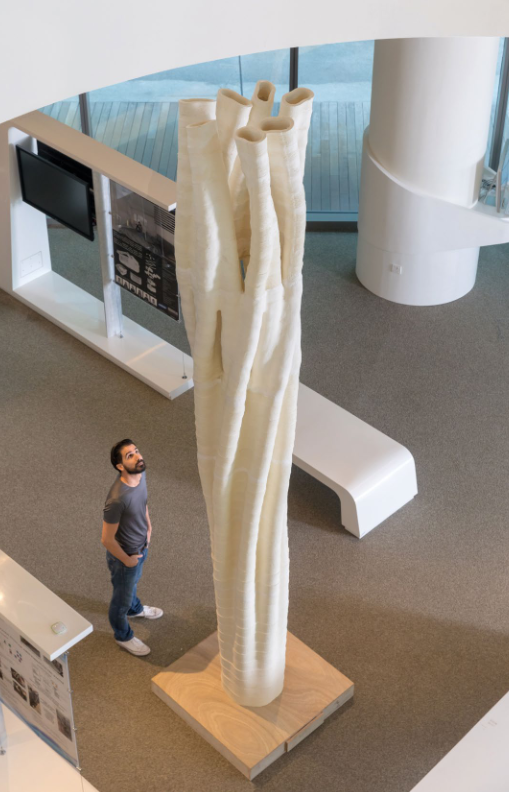
Source: Singapore University of Technology & Design
The amount of time required for printing was 60 hours with total wet material weight was 480kg and cured weight 105kg.
The cost of materials was £220 | £2.1/kg.
Inference
The current research into alternative materials is at the point where their viability on an architectural scale is still very unpredictable and their properties uncontrollable; the materials strongly dictate some of the design and fabrication parameters.
But, the kind of approaches we look into today are definitely on the verge of changing construction — construction that we comprehend and correlate to.
Everything on the planet is continually evolving and construction as a whole is approaching a point in its development where these kinds of scrutinies and experiments have become a necessity. A necessity in progressing our role as humans on this planet and the symbiosis between ourselves and the environment around us.
Make Shift: Manufacturing And Fabrication With Bio-Inspired Materials is a project of IAAC, Institute for
Advanced Architecture of Catalonia developed at Master in Robotics and
Advanced Construction in 2021 by:
Students: Mit Patel, Robert Blackburn, Vincent Verster
Faculty: Mathilde Marengo
Special thanks to:
Mark Lepelaar – NPSP
David Andréen – Lund University
Yadunund Vijay – Open Robotics, Singapore
Sources
npsp Nabasco
https://www.npsp.nl/
Interview with Mark Lepelaar
Pulp Faction
https://discovery.ucl.ac.uk/id/eprint/10094460/1/Fabricate-2020.pdf
https://www.researchgate.net/publication/355394603_
https://www.researchgate.net/publication/355394603_Transcalar_Design_An_Approach_to_Biodesign_in_the_Built_Environment
Interview with David Andréen
Cellulosic Biocomposites For Sustainable Manufacturing
https://www.researchgate.net/publication/325577233_Large-Scale_Additive_Manufacturing_with_Bioinspired_Cellulosic_Materials
https://www.nature.com/articles/s41598-018-26985-2
https://discovery.ucl.ac.uk/id/eprint/10094460/1/Fabricate-2020.pdf
Waste Statistics
European Commission. European Construction Sector Observatory—Improving Energy and Resource Efficiency; European Commission: Brussels, Belgium, 2018. via
https://www.mdpi.com/2071-1050/12/19/8096/pdf
https://www.unep.org/interactive/beat-plastic-pollution/
https://datatopics.worldbank.org/what-a-waste/tackling_increasing_plastic_waste.html
https://www.epa.gov/smm/sustainable-management-construction-and-demolition-materials
https://www.epa.gov/facts-and-figures-about-materials-waste-and-recycling/advancing-sustainable-materials-management
https://cdn.odi.org/media/documents/odi-et-cp-construction-report-sep20-proof04_final2.pdf
https://www.researchgate.net/publication/318567844_Production_use_and_fate_of_all_plastics_ever_made
https://www.sciencedirect.com/science/article/abs/pii/S0959652612002314
https://books.google.es/books?hl=nl&lr=&id=v5alDwAAQBAJ&oi=fnd&pg=PP10&dq=re+use+atlas&ots=18lpx0Zuad&sig=rRbv1o2zdnwOs6cSo1GNha01sJk#v=onepage&q=re%20use%20atlas&f=false
https://www.nationalgeographic.org/article/plastic-bag-found-bottom-worlds-deepest-ocean-trench/
https://time.com/3669084/plastics-pollution-fish/
https://www.nature.com/articles/d41586-021-01143-3