“[] architecture has always wanted more –to be one of us, self-aware, pulsing with life; it has always sought to mimic the living”
-Living Bits and Bricks, Alex Haw, Carlo Ratti, AR, May 2012
Our objective in this project is to create dynamic relationships between structure, environment and human, by engaging new technologies and smart materials in our design. Our goal is to find the equilibrium where digital concepts intertwine with physical structures and how physical structures can enhance the environment as well as human perception and activity.
We reconsider the mechanisms of kinetics in an environmental and human responsive structure where smart materials are completely embedded. We introduce Shape Memory Polymer as our case study of smart materials.We are looking for a programmed surface which reacts to wind and human decisions. Our concept is resumed to an interface system which stores real time local wind data and proposes optimum surface transformations for ventilation of space. The user is able to choose the shape and the form of transformation as well as set his own needs so the system would propose new solutions.
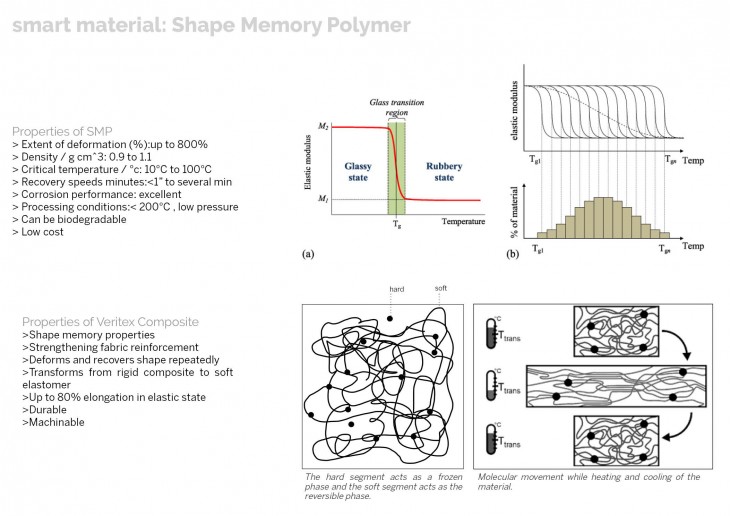
SMP properties
SMPs possess two material phases. The glass and the rubber phase. In the glass phase, the material is rigid and cannot be easily deformed. When the temperature is greater than “Glass transition temperature”, the material enters the soft rubber phase and becomes easily deformable. SMP recovers by heating the material above its glass transition temperature.
In the glassy state all movements of the polymer segments are frozen. The transition to the rubber-elastic state occurs upon increasing the thermal activation, which means that the rotation around the segment bonds becomes increasingly unimpeded. In this elastic state, a polymer with sufficient molecular weight stretches in the direction of an applied external force. If the stress is applied for a short period of time , the entanglement of the polymer chains with their direct neighbors will prevent a large movement of the chain. So when the external stress is released, the sample recovers to its original length. If the stress is applied for a longer period of time, then a relaxation process will take place which results in a plastic, irreversible deformation of the sample because of slipping and disentangling of the polymerchains from each other.
SMP can be activated by temperature,pH and light. In this project, we focused on temperature as it is the most appropriate method for this specific polymer. In our first experiments we used heatgun; however it couldn’t offer us a continuous, uniform stream of hot air. Our next move was to use nichrome wire: Nichrome wire is an alloy commonly used in heating devices, which it increases the temperature when electrical power is supplied. As the current travels through the nichrome wire, the resistance creates a voltage drop and, in turn, heat (P = I2 *R). We coiled nichrome wire (0.03mm) around the SMP and we manage to get uniform and precise heat. The length of the wire used, as well as its thickness depends on the size of the SMP. The distance between coiling depends on the need of deformation.
Actuators are characterized as the forces which deform the SMP after its heated and becomes flexible. There are multiple ways to change SMP’s shape; for this project we deformed the SMP by hand, by pulling with strings and by using soft robotic muscles.
The decision to use soft robotic muscles was made due to their great properties as actuators. They are flexible and light, they expand in a high percentage in relation to their size, they present mechanical properties and the angle of deformation can be controlled
(max almost 360 °.). The challenges for using soft robotic muscles is finding the right proportion between the pressure needed to initiate movement against the resistance of the members. Also finding the right kind of membrane stiffness which does not explode with the amount to actuation soft robotic muscle casted with ecoflex silicone pressure. In this case we eliminated the thickness of the soft robotic muscle to zero. The thickness of the first layer remained the same (3mm) while the top layer is now 1mm. Different shores of silicone were also tested so as the soft robot muscle presented different behaviors. We observed that the muscles did not have enough force to actuate as they were weak. With increase in pressure the soft muscles exploded.
wooden mold frame applied on a surface
_silicone is poured into
_after it dries, a stensil is applied on top
_spray with hydrophobic spray
_remove the stencil
_pour second layer of silicone
Having already studied the way SMP can be activated as well as multiple actuators, we need also to test the properties that SMP has as a smart material. This research includes testing the polymer as far as its shape memory, tensility and mechanical performance. The Shape Memory Polymer which is used in all experiments is the Veritex Composite.
In those experiments, SMP was tested for pulling and pushing weight. In both set of experiments, the SMP was placed as a joint both in the inner and outer angle of the wooden sticks. In the case of small wooden sticks the SMP performed as expected. When longer and heavier sticks were tested, the recovery of the SMP was not the same. Also, there was a difference in the duration of recovery state. In conclusion, the SMP can push weight quite easily, but when it comes to pull the same amount of weight, it is not strong enough to obtain a 100% its primary shape.
In these set of experiments, a combinationof simple geometries were also testedbut now wooden sticks are crossed with a double SMP joint. In all three cases the SMP obtained a total recovery, however, there were some differences in time as seen on the comments. Gravity
is a factor that affect the memory effect of the SMP. When the SMP has to pull weight against gravity, its performance is not efficient.
Following the complex scissors geometries, these experiments test SMPs placement in a row. We design a strip from three pieces of polypropylene, a material light and flexible while the SMP pieces were placed on the valleys of the design. First, one SMP was tested, while later, multiple SMPs were placed in every valley in a variety of combinations rotating to x axis. The target was to observe the deformation of the stripe which could lead us potentially to a surface organisation. The experiments were successful, as the SMP was strong enough to retain and push the stripe back to its initial position. The initial deformations were made both by hand and strings.
The step forward to the previous experiment is to translate a continuous strip to multiple modules. Now the SMP acts as a joint and not only as an indepedent component to a set geometry. During the experiment, the friction between the module and ground caused a great degree of resistence in SMP performance. When a smoother slide was achieved, the SMP recovered 100% to its initial position. However, the geometry was problematic: because of the weight of the modules and their small width, occasionally they were falling on the sides. That brought the need to create a supportive grid in two dimensions to support and keep in place the strips performing.
By testing the SMP in multiple geometries and directions, we became familiar with its mechanical properties:
>When it reaches its glass transition temperature its strength is small: it cannot carry weight more than 1kg. On the other hand, when the SMP is in room temperature it is an excellent retainer of weight and strength.
>Gravity is stronger than the pulling strength of the polymer: this means that the SMP can push towards gravity (because gravity is in favor of the movement) but it cannot pull weight against it. If different directions are combined, then the performance of the SMP is improved. As far as the activation is concerned, the nicrome wire is the most suitable as it offers precision and control of the heat as well as the possibility to connect multiple SMP together: electricity can equally be distributed through a series and parallel circuit.
After our last experiments with geometries which could potentially shape a responsive surface, we end up with the conclusion that our research should focus in three main topics:
-research of the optimum SMP use as a joint
_research on strong but controllable actuators
_design focus on linear structures
The final material system combines five different layers: the SMP coiled with the nicrome wire, the wood sticks, one polypropylene live hinge, one layer of silicone and the soft robotic muscle. The way they were joined together is via revits. The revits are used because of their ability to keep the layers together without moving (an issue we confronted with screws) as well as their light weight. The reason which led us to this solution was to achieve the best performance of both the SMP and the soft robotic muscle at the same time, eliminating any resistence, keeping the parts together and connecting them with a supporting frame.
The design process concerns a study of organisation of space in grid. The objective is to enhance wind from the maximum possible directions. The way the joints are arranged in space would shape this system while their performance will release an organisation in adaptive panels. The gaps between them would be filled from fixed components, while this system would be supported by a framework which will host the necessary technical equipment.
Some of the triangular panels which cover the grid are fixed, some other are moving according to the wind flow, as explained
before. The attached wooden sticks have the maximum possible weight that the muscle and the SMP can pull and carry, and dimensions which can support and lift the skin a panel 50*50cm. The fixed panels are wooden (mdf 2,5mm) while the adaptive are supported from the joints and covered with silicone sheet. The performance of the panel concerns the opening of the angles rather than the sides of the triangular shape.
When wind comes from a certain direction, an interface provides the necessary data so joints are activated to open the panels. Each panel works individually but at the same time connected in a larger system which permits the channeling of the wind in the whole area of the surface. The panels which will open or stay closed depend on the air and the electricity provided to the muscle and the SMP. If the SMP is heated then the muscle deforms it. If not, then the panel stays closed as the SMP retains its position no matter the soft robotic muscle activation.
With the use of Processing an interface was developed which based on the location, will inform the system for the best solution to regulate the comfort zone through natural ventilation. What we aim for is a programmable skin where the user could also participate and express his own needs and desires. While the interface receives real time environmental data and proposes the optimum solution for temperature regulation, the user is able to change the results by introducing his own standards of comfort zone. The improvement of this interface can lead us to a complete calculation and control of environmental factors (natural light, rain collection etc)
This skin can be applied in different conditions and buildings; it can be used as a ceiling, as a facade or as a combinations. Furthermore, with an improved structural adaptation it can also stand on its own as a pavilion. The design allows adaptations as far as the scale of the panels and their position is space is concerned: multiple and different parameters can be applied on depending the use and the environmental conditions of specific locations on the map.
Response_able 2.0 is a project of IaaC, Institute for Advanced Architecture of Catalonia
developed at Master in Advanced Architecture 01 in Digital Matter – Intelligent Construction Research Line in 2015-2016 by:
Students: Nikolaos Argyros, Maria-Klairi Chartsia, Sameera Chukkapalli, Jakub Havlik
Faculty: Areti Markopoulou, assistants: Alexandre Dubor, Angelos Chronis