IAAC – Master in Robotics and Advanced Construction
Workshop 1.2
Faculty: Eduardo Chamorro
Faculty Assistant: Marielena Papandreou
FABRICATION DESIGN STRATEGIES
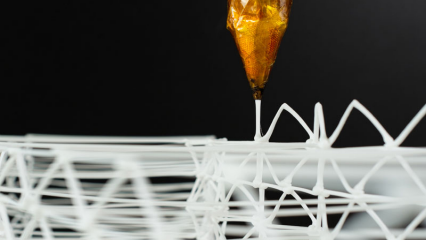
Credits: ETH -Gramazio Kohler
Syllabus
Rapid prototyping and advanced manufacturing are fundamental technologies that enable an integrative conception and production of fabrication-informed material and structurally informed design processes. Additive manufacturing (AM) techniques in architecture are mainly deployed through layer-by-layer or contour crafting. Nowadays there is a global collective drift towards the development of a fabrication-informed, adaptive, non-standard architecture.
This intensive workshop will focus on designing and manufacturing spatial non-standard large-scale lightweight structures that outperform the usage of material per load capabilities through robotic additive manufacturing. During this period, students will be challenged to demonstrate their ability in Design for Manufacturing with a robotically 3d printed model of a structural element, intended as a scale bridge in an iterative process of idea generation, fabrication prototyping, reiteration, analysis and learning.
While the seminar and workshops of the MRAC first term focus on tools and abilities exploration, this workshop keeps a horizontal approach to design, tools and techniques from a trans-disciplinary point of view. We will challenge ourselves to design a “lightweight”/efficient structure, with spatial frames, and stress forces path planning strategies, not only in the concept of using the least amount of materials but also by adapting the material deposition to be balanced out between the original geometry and the most performative one.
Learning objectives
The objective of the workshop is to prototype, fabricate and test simple structural models through robotic non-planar additive manufacturing. With an overview of the state of the art in Additive manufacturing spatial frame syntax and its influence on the structural capabilities. Discuss the practical implementation of custom end effectors, and brainstorm to later produce the most performative structural model with this technology. At course completion the student will learn:
- Design for manufacturing as one single goal strategy
- Communication between ABB arm robot and custom end effector
- Specific workflows from structural nonplanar additive manufacturing strategies
- How to structure capabilities informed by geometry and materiality
- How to calibrate/adjust end-effector tools and possible modifications of them
- To author and prototype robotic additive manufacturing path planning strategies
- To think independently about novel robotic workflow concepts and implement them in small groups.