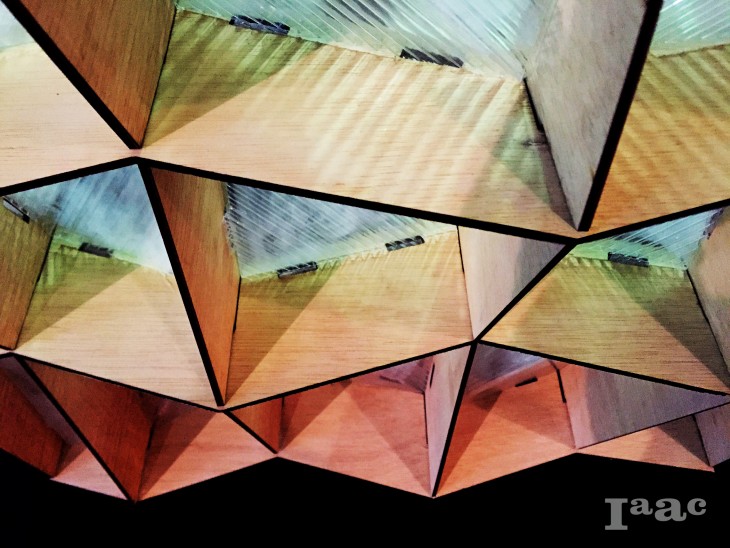
Joint close-up
The term Compound Structure refers to a structural configuration with no apparent hierarchy between materials. Instead, two or more materials are integrated in a way that all parts are mechanically activated with the objective of optimizing material usage. This digitally fabricated module unifies two very distinct materials to form a structurally integrated facade module by combining the mechanical ductility of plywood with the lesser known excellent strength-to-weight ratio of cellular polycarbonate.
Front elevation
Apart from its mechanical properties the module is highly apt for architectural application because it is based on a parametric system set up around the filtering of light and solar radiation. The parameters (spacing between slats and rotation of slats) can be adjusted in both the horizontal and vertical direction to optimize the energy and light performance of the building.
The excellent light diffusing properties of cellular polycarbonate comes as a bonus and was demonstrated by projection mapping during the final presentation:
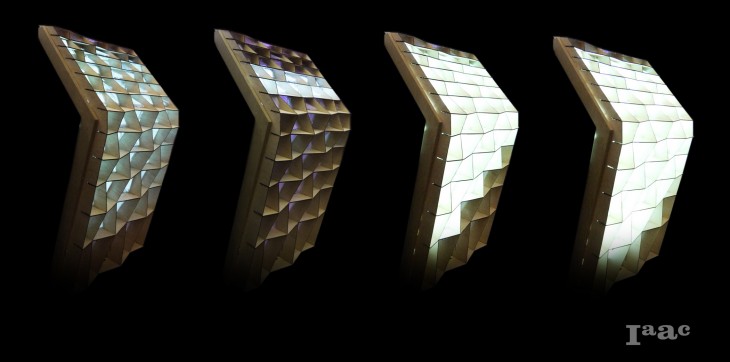
Projection Mapping – Light Testing
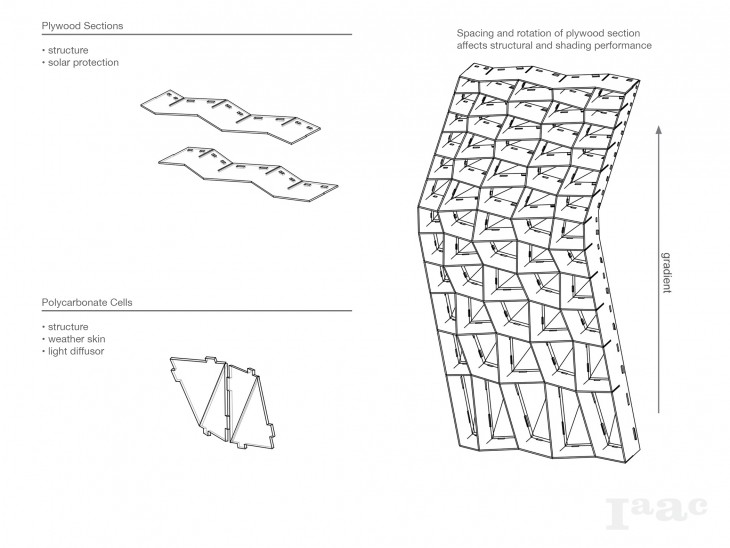
Facade Components
Technical Description
Technique: sectioning
Material 1: 4mm plywood
Material 2: 6mm transparent cellular polycarbonate
Ratio: 35-65
The module can be described as a triangulated mesh, formed by a grid of plywood contours with cellular polycarbonate sheets as panels in the grid cells. The mesh has a gradient of cell size, with the largest placed at the bottom and the smaller at the top, meant as a measure against high solar incidence during summer. The polycarbonate panels have been sliced on one side only to permit bending while keeping the piece together. The panels are placed on the inside of the panel in order for the horizontal and vertical plywood sections to double as solar protection. The horizontal plywood sections have been given a 15 degree rotation downwards to lead rainwater away from the joints.
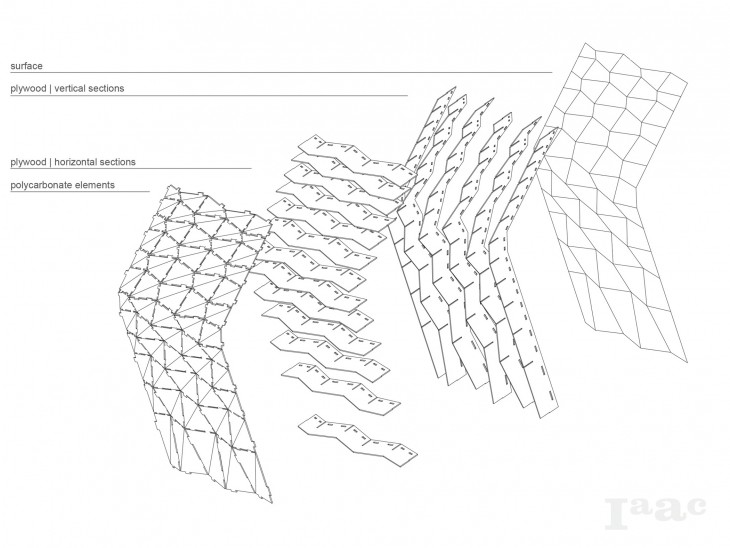
Facade Composition
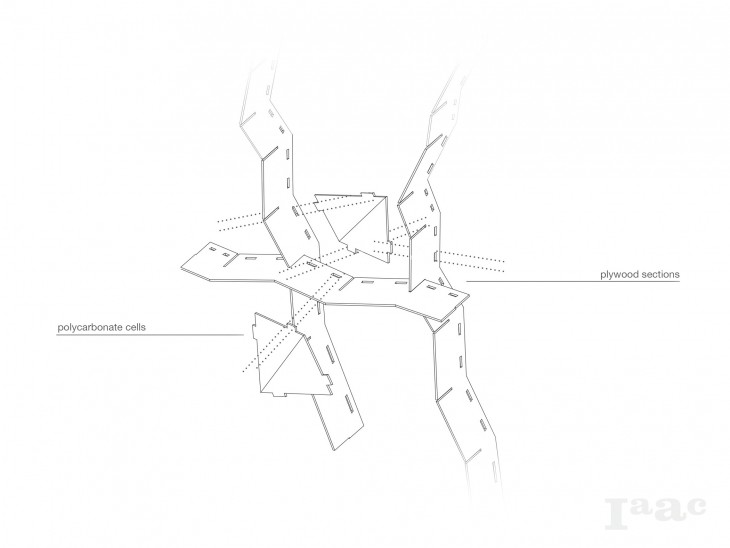
Joint Detail
Digital Fabrication Process
The plywood sections are put together using press fit joints, all cut with laser. Some of the shorter horizontal pieces we cut using an Epilog laser, while the longer vertical pieces were cut on a large industrial Multicam.
The polycarbonate pieces were milled using a Shopbot with a 6mm, single flute milling head. For the milling, an acrylic sheet was screwed onto the Shopbot bed. The polycarbonate sheets were attached to this sheet using double sided tape, ensuring that each piece was safely secured and to prevent them from flying around during the milling. For the outline of the pieces we milled with 8mm depth and for the diagonal engraving we milled at 3mm.
The assembly process proved to be the most challenging due to the rigidity and brittleness of the polycarbonate. We also realized that for the same reasons our tolerances were too “tight”.
Compound-Structure Facade Filter is a project of IaaC, Institute for Advanced Architecture of Catalonia developed at Master in Advanced Architecture in 2016 by:
Students: Maria-Klairi Chartsia, Sidharth Kumar, Peter Geelmuyden Magnus, Ekaterina Simakova
Faculty: Alexandre Dubor, Djordje Stanojevic